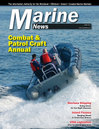
Page 28: of Marine News Magazine (June 2015)
Combat & Patrol Craft Annual
Read this page in Pdf, Flash or Html5 edition of June 2015 Marine News Magazine
COLUMN LUBRICANTS surfaces and provides separation. It is this separation that make an informed purchasing decision prior to ? lling the helps protect the surfaces from wear, pitting, and scuf? ng. system/gearbox.
EHD ? lm thickness is a function of speed, pressure, sur- A preferred method is the standard test method CEC L- face condition, temperature, and viscosity. 45-A-99, also known as the KRL Tapered Roller Bearing test.
A reduction in viscosity, either temporarily or perma- Used by OEMs and lubricant manufacturers, this test simu- nently will reduce the lubricant’s ability to create a ? uid lates lubricant performance under shear stress in actual gear ? lm to separate the shaft from the bearing. Thrusters oper- and bearing applications. It is considered the most severe of ate under extreme loads as they transfer power generated by the available shear stability tests and offers the best correlation the vessels engines, through the bevel gears of the z-drive to actual ? eld performance. The CEC L-45-A-99 test simu- and on to the propeller. When the correct viscosity is not lates a high shear condition to accelerate the breakdown of oil maintained, an increase in micro-pitting and gear wear may viscosity. To accomplish this, tapered roller bearings are used occur. The lubricant selected to protect shafts, bearings, because the large surface area of the roller exposes the oil to a and gears must be able to withstand high shearing forces. high percentage of shear. The test bearings are run at 1,450
In practice, a good sampling program can be used to rpms for 20 or 100 hours under a load equal to 5,000 N, at monitor the condition of the oil. Tracking the viscos- 60° C. The results are calculated by measuring the percent- ity over time will detect loss of viscosity due to shearing. age of viscosity change between the oil viscosity pretest and
That’s why monitoring trending data is part of a successful the oil viscosity post test. A small value indicates a high shear oil analysis program. The condition of oil should always be stability, while a high value indicates poor shear stability. checked against a representative baseline. A baseline can be established by directly sampling the sump soon after ? lling R T S S
ESULTS OF ESTING HEAR TABILITY with fresh oil and after a short duration of operation. The Internal testing of various EALs using the test method frequency of sampling is typically established by the OEM CEC L-45-A-99 has produced a wide range of results among or depending on the application and operating conditions. the sample lubricants. Synthetic ester based products that did
An adequate interval is typically based on the number of not use viscosity modi? ers produced the best results. Even service hours or at set intervals to check for viscosity sta- after a short test duration of 100 hours, two of the samples bility. If one of the tested parameters ever falls out of the with viscosity modi? ers showed a minimum of 50% loss in
OEM recommended range for the equipment, it should be viscosity. However the two oils that were formulated without replaced and a new baseline should be established. viscosity improvers maintained a consistent viscosity.
While an oil analysis program will help accurately mea- Even a small drop in viscosity can drop the ISO viscosity sure how the current oil is performing, there are numerous grade down into the next VI category permanently. Running tests that a manufacturer can perform in the lab to char- too light of an oil viscosity can reduce the lubricant’s ability acterize the oil performance to help the OEM or end user to provide a suf? cient oil ? lm. If this occurs, lubricant protec- tion is compromised, leading to higher proba- bility of premature wear, scuf? ng, and pitting.
ONCLUSION
C
EALs are formulated to protect the environ- ment. But there is no need to select an EAL that compromises the protection of thrusters or shaft bearings. Careful selection of EALs is necessary to prevent failures of bearings and gears. Protecting against shearing stresses is achieved by selecting EALs with a high VI.
But lubricants that employ viscosity modi? - ers to raise VI can compromise shear stability.
Selecting an EAL using a base oil with an in- herently high VI – assisted by a logical sam- pling program – will ensure the high level of shear protection that meets today’s environ- mental and equipment requirements.
June 2015
MN 28