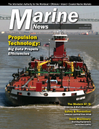
Page 41: of Marine News Magazine (July 2015)
Propulsion Technology
Read this page in Pdf, Flash or Html5 edition of July 2015 Marine News Magazine
Testing has revealed that the most signi? cant damage comes from abrasion of the rope when under load and transverse pressure. This speci? cally translates to damage of the rope over time where it contacts the ? anges of the hoist drum at layer transitions. The combination of line pull and transverse pressure from the stored rope create a “scrubbing” that will eventually wear the rope. This can be mitigated with improvements to drum surface conditions and also by changes the position of the rope on the drum periodically. By knowing the mechanism and being able to visually inspect the rope, the damage can be addressed before it becomes an operational issue.
Critics Converted with
Measurable Differences
Since its introduction, KZ100 has the attention of the on his gloves, clothes or other parts of the equipment. industry. While it’s an industry that is vested deeply in wire Additionally, traditional lubricating oils will attract dirt rope usage as a standard, even the most skeptical critics and particulate that can also create challenges. The torque are recognizing the bene? ts. When most people think of neutral construction virtually eliminates load spin and ca- synthetic rope, the image that comes to mind is the tradi- bling. While crane operators have found ways to address tional nylon or polyester ropes. The foundation of KZ-100 this challenge safely with wire, with KZ100, there are no is very different. It is made from high performance ? bers extra steps, special attachments or procedures required. It that have very high strength, low weight, and low elonga- is inherent with the product. tion. This provides a rope that is comparable to wire in The product is more formable in nature and does not strength, size and elongation. For example, KZ100 at a have a shape memory. This means that damage from kink- 22mm (7/8”) diameter has a breaking strength of 84,000 ing or crushing is not a concern. Bending the rope will not lbs (38.1t). When used at a 5:1 safety factor, the maxi- cause the strands to “break.” mum elongation seen will be 1.3%. One of the largest mental hurdles is the inspection and
When some stakeholders ? rst hear of synthetic rope tech- retirement method. Since the rope is made from millions nology, they picture a fragile product that is easily damaged. of ends of ? bers, you cannot count broken ends in the
However, with today’s ? ber, coatings, and rope construction same fashion as is done with wire. Samson has developed technology, Samson’s similar rope products are used for tank- a visual inspection tool that provides the user with various er ship mooring, tug boat applications, mining applications, levels of wear that are considered acceptable and those that offshore heavy lift slings, and military applications. The ? ber require retirement. This work is supported by a continuing technology is used for bullet proof vests, vehicle armoring, robust residual strength testing program. and cut resistant gloves for glass handling operations.
Beyond the base technology, the skeptics are learning It’s Not New, Just New To You that the assumptions and accepted practices with wire rope While the technology is new to the crane industry, it is not are not the same with synthetics. There are few areas where new to high risk, demanding applications. In each indus- the differences are immediately noticeable. First, the han- try serviced by Samson, project timelines are critical, safety dling and reeving is much easier. Due to the signi? cant is paramount, and the investment is extensive. It won’t be weight reduction, the effort expended by the operator to long, and the idea won’t seem foreign at all. Instead you’ll be handle the rope is much lower. Also, given the more ? ex- saying, I can’t believe we didn’t do this sooner. ible nature of the product, the force needed to manipulate
Michael Quinn is the Director of New Business the rope is less. This equates to more time lifting and a
Development for Samson Rope Technologies reduced risk of hand or back injury.
in Ferndale, WA and has worked for Samson
One of the other immediate differences is the lack of for 7 years. Michael has a background in lubricant on the rope. This means less maintenance cost
Metallurgical and Materials Engineering, in time to apply lubricant and cost of the materials. How- operations management and sales/marketing.
ever, it also means the operator is not getting grease/oil 41 www.marinelink.com MN