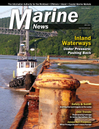
Page 58: of Marine News Magazine (May 2016)
Inland Waterways
Read this page in Pdf, Flash or Html5 edition of May 2016 Marine News Magazine
CORDAGE & RIGGING one, so in those cases the material was a of 300 pounds — would need to move nonstarter. too. And although cranes and forklifts • Stretch: Because some lifts would were available to help, it was often take place under ceiling-height con- faster to get a couple of workers together straints, the slings used needed to exhibit to drag the heavy hardware over to the low and predictable stretch levels. The next spot. Over time, the bodily stress in- shipyard needed to be assured that any volved presented a threat to the workers’ constructional elongation would take ergonomics and health. place in the manufacturing stage, and • Ef? ciency: In the outdoor yard, that they’d ultimately be delivered a even heavier lifts were taking place. product with very low stretch and a load Whereas the indoor slings were han- curve as predictable as that of steel. dling loads up to 30 tons, slings in the yard were rated for 60-, 80- and 100-
To that point, a synthetic solution ton picks. The weight of these slings that alleviated all of their concerns was beyond even a team of the strongest had never existed as an option, and workers, so they had to rely on the slow so they relied on steel. But steel had strength of cranes to move the hard- some heavy drawbacks too. ware from spot to spot. Here, the weight wasn’t just an ergonomic issue; it slowed
FRUSTRATION WITH THE down productivity too.
STATUS QUO • The Elements: Naturally, every-
Prior to adopting Fortis², the ship- thing outside on a shipyard is vulnerable yard’s assembly areas were strewn with to salty ocean air, rain, sleet, snow and enormous, heavy slings composed of more. When it came to the heavy-lifting steel wire and chain. As they contin- slings, the effects of rust, ice and corro- ued to build bigger, better and higher- sion were factored into the equation, tech vessels over the years, the lifting requiring frequent inspections and pre- slings brought workers at least three cautions to prevent accidents or failure. ever-present frustrations they were This further impaired ef? ciency and ready to leave in the past. also presented safety threats.
• Ergonomics and Employee Safety:
When large, heavy pieces of a vessel ar- FORTIS²: A Third, Better Option rived at the assembly building, riggers There had to be a better way. A safer would hoist them up onto the hull with and easier one, too. Intrigued by the cranes and steel-wire slings. When mov- challenge, Yale Cordage approached ing from one piece to the next, the lifting the shipyard. The task: to create a syn- slings — which weighed in at upwards thetic lifting sling that did everything
Fortis² Slings: advantages at a glance …
More durable than Stiff enough to push 80% lighter than traditional ? ber slings under objects comparable wire sling
One person able to lift Will not soak up water Will not corrode or rust eye to crane hook or freeze
May 2016 58
MN
MN May16 Layout 52-65.indd 58 4/20/2016 10:43:34 AM