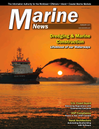
Page 27: of Marine News Magazine (February 2017)
Dredging & Marine Construction
Read this page in Pdf, Flash or Html5 edition of February 2017 Marine News Magazine
ity. Additional ? nancial savings not addressed in this busi- ness case include bene? ts derived from reduced welder ergo- nomic issues. Costs associated with over-welding, including additional man-hours, the increased ship weight, increased hours of material grinding in the case of rejected welds, and other variables were not considered in the calculation.
In the end, says Fanguy, the project team demonstrated core competency with key technologies and the capability to execute a complex, multidisciplinary development roadmap.
He added, “Signi? cant progress has been made in Phase 1 toward realization of a ? exible, ef? cient, high-productivity robotic welding solution for the U.S. shipbuilding indus- try. Opportunities to transfer this technology to additional shipbuilding and, broader defense applications continue to emerge. It is incumbent upon the Navy, shipbuilding indus- try, and U.S.-based suppliers of these technologies to provide a solution that will continue to place the United States at the forefront of innovation and manufacturing capability.”
Looking Back, Forging Ahead
Asked where the technology and robotic welding would provide the most value, Fanguy replied, “We believe that certainly it is better suited for series build, but the intention at Bollinger is to use this technology for part families that may not require a series build contract to exploit the savings from this technology. And, he adds, “Based on the high level of commonality between the part families and weld types among both Bollinger and other Shipyards, it appears that there are signi? cant technology transfer opportunities for technologies outlined in this assessment report.”
Pat David also thinks that the robotic approach has legs.
In fact, he insists, “One of the issues prior to this project when using robots for manufacturing that had high vari- ability was the amount of time that it took to program the robot to do the weld. Our ability to quickly generate that path – that information – is where the savings lie. So those past problems aren’t as valid as they once were. A lot of folks are going to reconsider this possibility now. Auto- mated welding is nothing new. But, the barrier to entry has been signi? cantly lowered with and due to this project.”
David continues, “The biggest obstacle, hands down, is the upfront capital investment.” And he agrees with Fanguy, saying, “This isn’t just limited to series-build hulls – one-off projects can signi? cantly bene? t as well. What used to take many hours for the programmer or the robot to generate a path for the welding now is exponentially faster than it used to be.” That’s good news for boatbuilders. As NSRP continues to lead, and shipyards and other stakeholders col- laborate, everyone wins. That reality has never been clearer.
*All images courtesy of SSI www.marinelink.com
MN Feb17 Layout 18-31.indd 27 MN Feb17 Layout 18-31.indd 27 1/26/2017 5:09:37 PM1/26/2017 5:09:37 PM