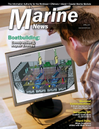
Page 48: of Marine News Magazine (April 2017)
Boatbuilding: Construction & Repair
Read this page in Pdf, Flash or Html5 edition of April 2017 Marine News Magazine
BOATBUILDING switch processes at the point of the work eters at the weld joint — at the wire Saving an hour each day saves time and is extremely bene? cial. feeder when using wire and advanced
For many shipbuilding operations,
All of these processes can be con- wire processes, and with a remote vessel fabrication typically begins in a trolled by the operator at the point of when using SMAW and gas tungsten shop environment before moving out- the weld with remote-control welding arc welding (GTAW) processes. side to the shipyard for completion. In technology. One advanced remote-
This reduces or even eliminates the both of these environments, a welding control solution on the market, Arc- need to walk back and forth to the operator could be several hundred feet
Reach technology from Miller Electric power source — often up and down away from the power source. The point
Mfg. Co., provides these capabilities ladders or scaffolding — to make of the weld may be in a dif? cult-to-reach utilizing only the existing weld cables welding adjustments. Not only does area of the vessel, or the power source and without the need for a separate this deliver signi? cant bene? ts for could be on a mezzanine or gantry. control cable. Eliminating the control productivity, but it also helps improve
Without remote-control technology, cable reduces the time and money that operator safety by reducing the risk an operator would need to walk back shipyards spend on maintenance, trou- for slips, trips and falls. and forth from the power source to bleshooting and expensive cable re- In addition, because welding opera- make a change to the welding process pairs. Eliminating time-consuming ca- tors can easily make the proper adjust- or to welding parameters. Time studies ble repairs and maintenance also helps ments to produce the best results, it show that it’s common for welding op- reduce the overall cost of downtime eliminates the need to “get by” with erators to change parameters or process- related to these repairs for a shipyard. less-than-optimal welding parameters es four to ? ve times per day, and often
The system provides operators will — resulting in improved weld quality more than that. Each trip to the power full control of weld settings and param- as well as productivity. source could take 10 to 15 minutes or more, and involve climbing ladders or stairs, or climbing through manholes.
Reducing or eliminating the need to make these trips to the power source can save an hour or more per welding operator each day in shipbuilding op- erations. Larger shipyards often have more than 100 welding operators on a jobsite, so the productivity gains and resulting savings can be signi? cant – adding up to thousands of dollars in time savings each year and justifying the equipment investment in remote- control technology.
Choosing a remote-control solu- tion that does not require a control cable also eliminates the downtime and maintenance cost associated with control cords. This cost can be signi? - cant and is often not accounted for.
Reducing Jobsite Safety Risk
Slips, trips and falls are among the most common causes of jobsite in- juries. Falls were the leading cause of worker deaths in the construction in- dustry in 2015, according to the Oc- cupational Safety and Health Admin- 48 MN April 2017