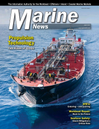
Page 48: of Marine News Magazine (July 2017)
Propulsion Technology
Read this page in Pdf, Flash or Html5 edition of July 2017 Marine News Magazine
SPECIAL REPORT: WORKBOAT REPAIR
The John W. Brown, one of two surviving fully operational Liberty ships, was launched in Baltimore on September 7, 1942. In 1983, Project Liberty
Ship acquired the Brown and, in 1988, moved the vessel to the harbor of her birth where it serves as a memorial museum ship. But, Liberty ships were not expected to last even five years; never mind 75. The longevity of the
Brown can be credited to many things – the all-volunteer crew that returned it to operating condition, for one. Another element includes the vintage ballast lines, joined so many years ago with Victaulic grooved couplings.
A six inch valve assembly that utilizes a grooved-end but-
Ballast Battles: no problem
The same bene? ts that Victaulic brought to that class of ter? y valve, grooved-end pipe and two rigid couplings to vessel long ago are no less important today. That’s because connect the components weighs approximately 35 pounds, representing a 58 percent weight reduction over the ? anged an estimated 60,000 vessels will need ballast water treat- assembly. Beyond this, a DIN 150 ballast line installed ment systems (BWTS) in the next ? ve years, and math- ematically, there is not enough yard capacity or skilled labor showed a weight reduction of 30 percent when Victaulic to meet expected demand. That’s where Victaulic comes in. was used instead of traditional joining methods. 52 slip-on
In 1942, speed and ease of installation was probably the ? anges, bolt sets and gaskets, versus 60 rigid couplings ac- most important factor in selecting grooved joining systems. counted for major weight increases in the welded/? anged
That hasn’t changed. More importantly, and although some system. Moreover, weight reductions by using grooved pipe couplings are achievable across a range of pipe sizes. owners remain unaware of this system, it isn’t anything new.
Shipyards that have used grooved couplings in place
For Jones Act tonnage ? eeing to Asian yards for a less ex- pensive ? tting, Victaulic manufactures not only here in the of ? anges on selected systems have recorded weight sav-
United States, but also in Mexico, Poland and China, as well. ings of 12 tons on OSV tonnage. The bene? ts of grooved
Wherever you go to re? t – or build from new – Victaulic technology can translate into more deadweight capacity, parts can be ef? ciently and economically obtained. But, what additional passenger load and/or less fuel consumption. if you are one of the 60,000 vessels that can’t ? nd dry dock It goes without saying that lighter assemblies are easier space? In that case, a Victaulic-enabled BWTS system might handle during installation and/or maintenance. After the fact, where excessive vibration can decrease the lifetime of be installed at sea, without having to deal with hot work.
a piping system, the elastomeric gasket contained within
In space-challenged pumprooms (where BWT equip- ment will be shoehorned), space is already at a premium. the grooved coupling reduces noise and vibration.
Finally, and with some estimates of BWTS installation
The reduced footprint of a Victaulic coupling will help costs reaching as much as $1.5 million USD (not to men- to ? nd room for BWTS equipment not originally envi- tion lost opportunity costs), a comparison of a DIN 150 sioned by a builder, ten years prior. In fact, Victaulic cou- pling’s 360-degree orientation capabilities, together with ballast line installed using Victaulic grooved products ver- sus traditional joining methods showed a 66 percent reduc- its smaller pro? le compared to a ? ange, make the installa- tion of grooved systems ideal for any con? ned space. That’s tion in installation time required (293 man hours). Time is because traditional ? anges are twice the outside diameter money, and every second spent unnecessarily in drydock is time that any vessel – in any trade – isn’t earning revenues.
of the pipe they are attached to.
Advantages:
Creates rigid, permanent, leak-tight joints in seconds Lighter than standard ? anging
No ? ame, arc or cutting oil / or hotwork permit needed Smaller volumetric footprint
Simple system limits extensive training requirements Faster than welding, traditional methods
Pipe joining can be accomplished while underway Time = Money (reduced installation time)
Elastomeric gasket & pipe grooving reduces leaks Reduced vibration
July 2017 48 MN