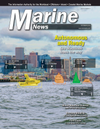
Page 44: of Marine News Magazine (October 2019)
Autonomous Workboats
Read this page in Pdf, Flash or Html5 edition of October 2019 Marine News Magazine
COATINGS
Proactive Removal of Copper hulls and designed to support anticorrosive systems in ma- from Antifouling Coatings rine applications. The coating is typically applied in two
When the International Maritime Organization (IMO) coats to ensure full corrosion protection. In addition to the ?rst instituted a ban on coatings containing tributyltin underwater hull, applicators used the epoxy on the vessel’s (TBT) due to its adverse effects on marine life, the U.S. Navy sea chest strainers, pump room strainers, waterjet tunnels, proactively anticipated the need for an antifouling coating engine exhausts and ride control ? ns.
that was entirely free of copper, which was a common biocide For added durability in the high-wear areas of the Mil- alternative to TBT. As a result, Sherwin-Williams developed linocket’s four waterjet tunnels, MSC selected Nova-Plate
SeaVoyage Copper Free in 2008 as a solvent-based, copper- UHS Epoxy, an ultra-high-solids epoxy novolac amine de- and tin-free ablative coating that protects against both soft veloped for immersion service. The coating offers superior and hard fouling. Its unique technology includes organic bio- protection compared to conventional epoxies, based on cides that are non-persistent in the environment, while the the coating’s advanced high-build, edge-retentive proper- coating’s low level of volatile organic compounds (VOCs) en- ties. Applicators ? rst applied Nova-Plate UHS Epoxy to sures compliance with stringent environmental regulations. the waterjet exhaust areas, followed by the anticorrosive
The copper-free coating provides an immediate environ- SeaGuard 5000HS Epoxy and the antifouling coating.
mental bene? t: when coatings containing TBT or copper are As the ? nal restoration steps, applicators applied Sea- polished, the metals leach off in the port and may adversely Voyage Copper Free to the vessel’s entire submerged and affect marine life. The biocides in the SeaVoyage Copper splash zone areas, including the underwater hull, sea chest
Free coating do not present similar environmental threats, strainers, pump room strainers, waterjet tunnels, transom while still protecting against a broad spectrum of fouling or- plate, engine exhausts and ride control ? ns.
ganisms. They simply degrade into non-toxic components in 24 hours in seawater, making the coating useful for re- A Win-Win Solution gions where maintaining water quality is a high priority. The SeaVoyage Copper Free Antifouling Paint checked
Sherwin-Williams quali? ed SeaVoyage Copper Free to all the boxes for MSC. The coating’s low weight and effec- the U.S. Navy MIL-PRF-24647 Type I performance speci- tive antifouling capabilities preserved the performance of ? cation as a copper-free antifoulant in October 2008 for the critical transport vessel, while also delivering durable a three-year life cycle. After further testing, the company performance for a seven-year drydock interval. SeaVoyage also quali? ed the coating for use on high-speed vessels that Copper Free also provided substantial environmental ben- travel in excess of 40 knots, as well as increased its expected e? ts due to its copper- and tin-free formulation.
performance cycle to seven years. Another bene? t of this The MSC’s need for speed doesn’t just apply to its maneu- technology is the coating’s lower weight, which is two- vers at sea. Sherwin-Williams Protective & Marine Coatings thirds the weight of traditional copper-based antifoulants. supported a tight timeline, enabling the USNS Millinock-
This lower weight provides improved fuel ef? ciencies for et to return to service quickly and freeing up the shipyard the Millinocket beyond what the coating already delivers for other assignments. Offering expertise related to speci- with its antifouling performance. ? cations, delivery and coating services, Sherwin-Williams helped MSC meet its turnaround goals. As the Millinocket
Total Protection Delivered continues its mission of transporting critical personnel and
The USNS Millinocket entered a shipyard for drydock equipment around the globe, it does so with con? dence in maintenance in January 2019. The shipyard and MSC in- the quality and durability of its underwater coatings.
spected the vessel’s underwater hull areas for damage, and the vessel was approved for minor spot repairs, followed by
Michael Manetta is Global Market Director – Rail, Marine and Power Gen- touchup coats of protective and antifoulant coatings and eration for Sherwin-Williams Protective & Marine Coatings. He has 15 years a full cosmetic antifouling coat on the underwater areas. of experience in the coatings industry with several sales and marketing roles within multiple end use segments. He is a NACE Coatings Inspector Program
Over the course of four weeks, crews applied a variety of (CIP) level III inspector. He can be reached at [email protected].
Sherwin-Williams coatings.
The primary epoxy anticorrosive coating applicators
Mark Schultz is Government Marine Project Development Manager for Sher- win-Williams Protective & Marine Coatings. He has 25 years of experience in used on the underwater hull of the Millinocket was Sea- the protective and marine coatings industry. He is an SSPC Protective Coatings
Specialist, a NACE Course Instructor for Coatings Inspector Program (CIP)
Guard 5000HS Epoxy. The coating is a high-performance,
Level I and Level II, and a NACE Certi