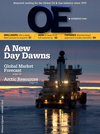
Page 63: of Offshore Engineer Magazine (Jan/Feb 2013)
Read this page in Pdf, Flash or Html5 edition of Jan/Feb 2013 Offshore Engineer Magazine
Underwater VehiclesUnderwater Vehicles 400ft. It also surveyed three partially enabled real-time monitoring and a stop while underwater. The crane then lifted decommissioned or operational sites, command if needed. the vessel and placed it in the Marlin producing 3D geo-referenced models. Marlin followed a predetermined cradle system on the utility vessel’s deck.
The frst survey for Chevron was survey route and used a sensor array to In the cradle, a hard-wired connection conducted 22 July and the last on gather point-cloud data as it circled the downloaded data Marlin had gathered. 7 August. Marlin and its docking cradle targeted platforms, spiraling deeper and Within 24 hours, Marlin software created and launch-and-recovery crane were deeper for complete coverage. It ran rough, 3D pictures of what Marlin had loaded onto 150ft-long utility boat 62 hours, and traveled 76 miles in seen. On two occasions, Chevron used
Lauren LaCoste in Port Fourchon, waters 26ft to 125ft deep. the early pictures for revisits.
Louisiana, and hauled to the sites. Marlin is rated to operate in waters as The data also was transmitted ashore, The crane lowered Marlin below deep as 1000ft. where teams created high-resolution, the surface of the water for launch. At the end of each survey, the AUV geo-referenced 3D images that were
Controllers on the vessel used acoustic returned to a rendezvous point. There it delivered to Chevron fve days later. All communications to start Marlin on used a nose-mounted, V-shaped tool to fnal reports were submitted within two its pre-programmed mission. The link capture the recovery cable autonomously weeks.
oedigital.com January 2013 | OE 65 oe_AUVs3.indd 65 03/01/2013 15:14