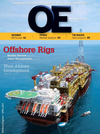
Page 71: of Offshore Engineer Magazine (Apr/May 2013)
Read this page in Pdf, Flash or Html5 edition of Apr/May 2013 Offshore Engineer Magazine
Subsea Tiebacks where necessary. In the rare case of a marginal chance they might need their own production. “We are also
Eyebrow wax deposits, LLOG has used chemi- it. It’s better to get $100 per barrel seeing more host facilities owned by cal solutions to reduce the cloud for your own oil than to get $4 per midstream companies, as opposed point or minimize wax deposits in barrel for processing someone else’s. to operators, for those reasons as the lines. “Thankfully, we’ve never That can create a diffcult situation well,” he says. really had to deal with any signif- for tieback producers.” Rick Rainey, spokesperson for cant asphaltene problems,” he says. Conversely, some host facilities Enterprise Products Partners LP,
To detect blockages, LLOG moni- are being designed larger than nec- agrees. The company’s Gulf of tors its operations in real time and essary for the current slate of wells, Mexico Independence Hub platform pays close attention to pressures by he says. The overbuilds are likely serves producers with a process- using subsea gauges at the well- due to host facility owners looking ing capacity of 800mmcf/d and its head and platform, among other to gain third-party PHA fees with- gas-volume capacity on its Indepen- procedures. “We typically install out giving up capacity needed for dence Trail pipeline is about 1bcf/d. a piggable loop where possible to facilitate the remediation of either a hydrate or a wax plug. If it’s a hydrate, we can blow that out from
SamSon takes the both sides. For wax, we can use the loop to circulate hot oil.”
Typically, LLOG integrates out of
HEAVY expandability into its system. For example, if a subsea manifold is heavylift required, the company will install a four-slot manifold, although only slings two wells are imminently planned. “That’s also useful for operations,”
Fowler says. “Every once in a while, we might get one tube of the umbili- cals that won’t work. Designing the system to be expandable gives us redundancy.”
At Who Dat, the company in- stalled four fexible risers with a two-loop system. During the project, one of the fexible risers was not available. By building in the loop
Greater Gabbard Project: The world’s largest wind farm. Seaway Heavy Lifting system, LLOG was able to begin ® installs turbine monopiles with Samson’s AmSteel-Blue lifting slings.
production as scheduled without waiting to solve the riser problem.
Third-party hosts
Going forward, Fowler sees possible
LIGHt SaFE FaSt EFFICIEnt constraints of third-party host production facility capacities.
Talk to the experts at Samson and put their experience and extensive
Many deepwater oil producers testing to work on your next heavylift project.
pay production facility owners a
Visit SamsonRope.com for the full case study on the processing and handling fee, about
Seaway Heavy Lifting/Greater Gabbard project.
$3 to $5 per barrel, to process, store and offoad their production.
“We’ve seen a lot of upward pres- sure on PHA fees,” says Fowler. “Recently, negotiations for frm ca- pacity have been challenging. Due to the current favorable oil prices, the companies that own host facilities
Visit us at OTC, Booth #8207 ®
IN THE RELIANT ARENA might want to keep that capacity for
Dyneema is a registered trademark of Royal DSM N.V. Dyneema is DSM’s high-performance polyethylene product.
their own wells, even if there is only oedigital.com oedigital.com April 2013 | OE 7373 oe_flowlines.indd 73 4/1/13 2:00 AM