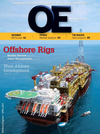
Page 74: of Offshore Engineer Magazine (Apr/May 2013)
Read this page in Pdf, Flash or Html5 edition of Apr/May 2013 Offshore Engineer Magazine
ators and fabricators are looking to pipelines and multiphase equip- lar approach to subsea equipment more novel concepts as felds move ment, and anything that can expand feld architecture. “I think of these into deepwater with feld pressures and contract as equipment is turned as building blocks,” says Skeels. as high as 10,000 to 15,000 psi. The on and off will have to be moni- “We try to make these systems cycle count from harsher environ- tored for maintenance management. in small blocks so that operators
Eyebrow ments and higher internal working In fact, regulatory entities will prob- can build whatever they need and
Subsea Tiebacks pressures are demanding thick- ably demand it as time progresses. deploy those from smaller vessels. walled risers, which can be very Materials-monitoring will be one of Modular design started catching heavy. “Just trying to hold them up the new industries in the future.” hold in the late 1990s, but now it with a foating surface vessel is ap- While deepwater production seems to be more important than proaching technical limits.” operations are exposed to high tem- ever. So we keep pushing to im-
As such, the equipment indus- perature and pressures, the trees, prove that.” try is working to develop new manifolds, jumpers and other sub- Going forward, the industry is go- riser materials such as carbon-fber sea hardware also experience rapid ing to continue to push the limits of composites to reduce riser weight. cool-down during shut-in or initial technology, forecasts Skeels. “The “These new materials seem to have start-up procedures, so the appli- industry is almost reinventing itself incredible weigh-savings, but we cation of very robust insulation is for HP-HT technology. All of the know little about how they react necessary to prevent the formation subsea equipment is interrelated, with wellbore fuids or chemical of hydrates and wax blockage in so improvement in effciencies treatment cocktails, nor how they fowlines. “We have been working and controls in every aspect will behave mechancially over a long hard to push the envelope on that,” become increasingly important.” period of time. And we have little Skeel says. Parker Energy Products, a divi- indication of what the tell-tale signs To help protect risers and subsea sion of Parker Hannifan Corp., are when their end-of-life is near,” tiebacks, FMC Technologies contin- also supplies tieback technol- says Skeels. ues its research on high-temperature ogy to LLOG and other deepwater
The industry needs to gear up versions of wet insulation. “We’ve developers, with tieback lengths on monitoring technology during been showing our Novalastic HT ranging from 300 ft to more than the next few years, to quantify the product, a glass-bead-impregnated 25 mi.installed in the Deep Gulf effects that motion and internal foam, at the Offshore Technology Condor development. The company wellbore production has on riser Conference and other shows. Cur- supplies 316L tubing for shallow performance in general, and new rent applications can work with water applications, Nitronic 19D materials in particular. As the num- wellbore temperatures up to 300 °F. zinc-coated tubing, seam-welded ber of HP-HT felds increase, the And we are looking at pushing super-duplex tubing for steel-tube effects of temperature and pressure performance to work in long-term fying leads and control umbilicals. spikes will need to be added to the applications at even higher temper- Parker has worked with LLOG since data collected from the fatigue by atures,” he says. the company’s frst subsea project water motion and vessel movement. Also, FMC Technologies contin- and continues to supply its Missis- “Drilling and production risers, ues its efforts to increase its modu- sippi Canyon development. “We run the traps to determine the specifc characteristics of the feld and life requirements, then make a case for the best material, best delivery, and cost-beneft ratio,” explains Craig Anderson, general manager for Parker. “There is a very limited supply of seam- less, coiled super-duplex tubing in the world, and again, based on the parameters of the feld, that material can be overkill. The seam-welded materials, which are more readily available, are slowly being accepted by the operators as they get more use
Anadarko’s 100%-owned in the water. Proper welding tech-
Constitution spar is the hub niques and better inspection pro- for the Caesar-Tonga feld cesses show that this can compete development.
Source: Anadarko Petroleum Corp.
against the seamless material.”
OE | April 2013 oedigital.comoedigital.com 7676 oe_flowlines.indd 76 4/1/13 4:23 PM