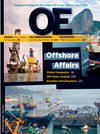
Page 62: of Offshore Engineer Magazine (May/Jun 2013)
Read this page in Pdf, Flash or Html5 edition of May/Jun 2013 Offshore Engineer Magazine
Decommissioning—
EPIC a view from the Southern North Sea conference
Removing platforms in the UK North
By Elaine Maslin
Its frst project was the 10-month-
Sea is a sensitive, costly process that
Innovating and being willing to do long decommissioning of the mini- can be made cost effective by develop- things differently could help save in mal production Welland platform, ing alternative methods.
excess of £100million of the cost of in winter 2011 (OE April 2011). The decommissioning its southern North facility’s 1000-ton topsides were away” from the facility and give
Sea assets, says Anglo-French inde- taken by transport barge to Vlissin- the crane barge contractor a wide pendent Perenco. gen (Flushing), Zeeland province, timeframe for completing the project,
But there is still plenty of scope for where they were refurbished before avoiding potential costly weather improvement, says Keith Tucker, being reinstalled off Cameroon with delays and enabling Scaldis to ft it decommissioning manager for the a self-installing jacket. The legs were into their schedule.
frm. In these early years the industry dismantled and recycled. Cutting the piles was carried out is probably over-engineering decom- A key saving on the project was internally with sections cut and missioning, he says. the use of a sheerleg lift barge (Scal- pinned to be lifted out with the same “It looks at this stage as if the sec- dis Salvage & Marine Contractors’ tool used for the cutting. Before the tor is over engineering decommis- Rambiz). This lift barge is usually lift, the cut piles were held in place sioning,” said Tucker. “Operations used during wind farm installations with suspended sleeves, so that it people working in decommissioning off Northern Europe - for the heavy was still safe to have men onboard or use the same processes of project lifts of both the topsides and jacket, walk away and leave the structure in appraisal. But decommissioning instead of a more expensive, larger, a safe state if the weather turned. structures is largely salvage. “ heavy-lift vessel. Despite early con- Another area to save costs is to
Perenco’s portfolio of assets—it cerns by the Health & Safety Execu- reduce the need for environmental has more platforms than anyone tive (UK regulator), the frm proved plugs in wells being abandoned by else in the UK North Sea—will all its case and transported the jacket on displacing the residual oil (left-over need to be decommissioned and, like the crane hooks instead of transfer- drilling mud) from the c annulus. many others in the basin, it is begin- ring to a transport barge, which Setting each cement plug costs about ning the process, with many felds reduced the spread required. £30,000. In some cases, that is being continuing for at least another 15-20 Perenco also pre-cut the legs for spent to seal in only a few dozen bar- years. the topside lift using 15,000 psi rels of oil-based mud.
However, the scale of the task waterjet, creating a beveled fnished On the three trial surface wells, means that Perenco has been keen to cut, so the separated pieces were Perenco managed to fush out the try out alternatives to make the pro- still “cupped” in place, and could be residual oil from the annuli which cess, a sensitive, costly exercise with held in position with a clamp. meant they did not have to put in a no returns, as lean as possible. This meant Perenco could “walk surface environmental plug before
OE | May 2013 oedigital.com 64
EPIC3_PerencoDecomm-Elaine.indd 64 4/22/13 4:56 PM