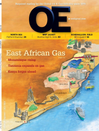
Page 42: of Offshore Engineer Magazine (Jul/Aug 2013)
Read this page in Pdf, Flash or Html5 edition of Jul/Aug 2013 Offshore Engineer Magazine
to the track were max 15% and 5%, strand jack, power packs for strand- The jacket was moved at 10m/hr and respectively. jack operation, motorized ballast the barge level was monitored continu-
The skid beam top surface was lev- pumps, 24 No’s (1000mt/hr) and 16 ously. Barge level was within 25mm eled within 6mm using shim plates No’s (250mt/hr), ballast line pipes, throughout the operation.
between the skid beam and sleeper mooring wires, mooring winches, etc. The jacket reached the fnal load- surface and then welded together. This The barge was made stern on, out location as it touched the stopper
EPIC — I ndia weld provided locking against the moored by lines and winches. Strand plate. Once sea fastening activities traction pull required during skidding wires were then pulled from strand were completed, the jacket was ready operation. The skid beam top was SS jack to anchor frame mounted on for sail out.
plate, stitch-welded over CS material the barge. A temporary platform was The MNP jacket was successfully and the mating surface was SS plates fabricated on the skid beam to facilitate launched in Mumbai High feld on with timber. FC strand-wire pulling operation. These 20January 2011. Successful comple- grease with slip coat innovations saved two days. The jacket tion of the launch jacket in record time was used as lubricant. During load- out, break-out was achieved with only was ready for load-out, once all the of 10 months demonstrated that new 270mt (2% of jacket weight). strand wires were laid down. A push- benchmarks can be established with
Load-out operation required four- ing bracket with 450mt push jack was proper coordination among teams, cli- strand jacks (900mt each), 34 strand welded to the skid beam. Strand wire ent’s support, calculated risks, proper wires (18mm) with SWL 15mt in each pre-tensioning began jacket movement. risk mitigation plans, and out-of-the- box thinking. Some innovative con- cepts that could not be implemented in this project can be implemented in future projects.
Acknowledgement
The authors wish to acknowledge the contribution of co-authors Mssrs. S. P.
Kulkarni, Dibyendu Das, Prabhas
Tripathi, Sandeep Badhe, Shardul
Samant, and Devendra Awadhiya during execution of the project and their assistance in the development of this article.
Mr. C.S. Kole is Chief
Executive of L&T
Modular Fabrication
MNP jacket ready for load-out.
Yard, Sohar, Oman and has been responsible for planning and execution of fabrication projects for L&T’s
Hydrocarbon Business at Sohar yard.
He has 32 years of experience and has successfully completed more than 30 major onshore and offshore projects.
Kole is a Civil Engineering graduate and gold medalist from University of
North Bengal.
Mr. Kumar Rudra is
Head – Projects and is responsible for L&T’s
Upstream Domestic Oil & Gas Operations. He has more than 22 years of experience and has successfully completed more than 12 major EPC projects. Rudra is a Chemical
Engineering graduate from Jadavpur Launch of MNP jacket in Mumbai High Field.
University Kolkata.
OE | July 2013 oedigital.com 44
EPIC4-India.indd 44 6/26/13 5:05 PM