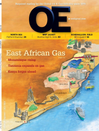
Page 44: of Offshore Engineer Magazine (Jul/Aug 2013)
Read this page in Pdf, Flash or Html5 edition of Jul/Aug 2013 Offshore Engineer Magazine
The Gryphon Alpha, which saw four of ten lines parted when it came off station in a storm in the UK North
Sea in early 2011, cost an estimated
US$1.8billion to reinstate, says Ma.
Production
Banff, with fve of 10 lines parted
Mooring line failures when it came off station in the same sector later in 2011, will cost an esti- mated $0.3billion. attract industry attention “Nan Hai Fa Xian (moored south east of Hong Kong), had four of eight
Mooring lines on foating production systems continue to fail, lines broken,” says Ma. “Plant [equip- costing the industry lost time and production— ment] was fipped upside down, pipe why and what is being done? reports. Elaine Maslin ruptured and all the risers broken. The message here is that the consequences of failure are high.”
However, when it comes to assess- ing the cause of mooring line failures, results have not been clear.
Research presented by Ma showed mooring chain accounted for the majority (47%) of all incidents fol- lowed by wire rope and then polyester rope. By number of breaks, mooring chain was still the primary cause.
Due to the high variety of root causes, from knotted chain, to fatigue and corrosion, fnding trends is “chal- lenging.” Worse, more than half of the root causes were surprises—unex- pected issues, hard to pre-empt.
But when failures do occur, Ma says they are often then repeated in a simi-
The FPSO had a chain failure near the anchor and Dalia lar area on the same installation. another failure in the same area two years later.
“Dalia had two chain failures near the anchor; [the second break two years after the frst] almost exactly he use of foating production 23 permanent mooring failures since in the same location. There are more systems in the offshore oil and 2000, and four of those were catego- examples of multiple breaks in the gas industry has been predicted rized as catastrophic, with riser failure same place. In your design, you are
T to grow at a signifcant rate between and extended feld shut-down. going to have a weak point and that now and 2017. In addition, at least 20 foating weak point is going to be in your moor-
The number of newbuild units production systems (FPS) had integ- ing lines and you are likely going to coming onto the market—on top of rity issues requiring intervention have similar failures in other lines.” conversions—is expected to peak in and 150 mooring lines were repaired Another trend is early-life failure. 2016 and 2017 (OE April 2013). or replaced across 33 FPS, says Sai “There is a clear trend of ‘infant mor-
However, the number of mooring- Majhi, of Granherne. tality’,” says Ma. “So many incidents related incidents involving foating “We are having too many [repeated] happen in the frst fve years (12 of the production units continues to raise mooring failures,” says Ma. “In 2011, 23 assessed).” concerns in the industry. we had four and when preparing this Majhi’s research showed a similar
Kai-Tung Ma, of Chevron Energy paper, there were another two chain trend, with the replacement rate of
Technology Co., says between 2001 failures and one wire rope failure, so it mooring lines peaking in the frst two and 2011, there were 21 mooring is ongoing.” years (about 50 of those assessed since failures—an average of more than The consequences of multiple moor- 2000), falling to just under 30 in the two per year (OTC.13, paper OTC- ing line failure can be high, says Ma. ffth year, before slowing increasing 24025-MS). Nine were multiple-line It is not just the mooring lines that towards the 20-year life of the system. failures. break—risers and other subsea equip- There has been work on improving
Research by Granherne, a KBR ment can be damaged, making rein- mooring integrity in the past decade, company, (OTC.13, OTC-24181), lists statement costly. including the SCORCH (seawater
OE | July 2013 oedigital.com 46 046_OE_0713_OTC-MooringFail.indd 46 6/25/13 1:13 AM