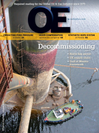
Page 55: of Offshore Engineer Magazine (Aug/Sep 2013)
Read this page in Pdf, Flash or Html5 edition of Aug/Sep 2013 Offshore Engineer Magazine
The replacement module would be landed using a water-dampening system and would then be landed out on extended hydraulic cylin- ders. Final mat- ing of the vertical connections is then performed by retracting cylin- ders, all controlled using an ROV at a hydraulic power panel.
Once the instal- lation and com-
Raimund Bjordal, technical missioning is lead, subsea processing intervention, complete, the
Statoil.
Credit: UTC2013.
SPI vessel would recover the mod- ule, waiting to be refurbished, up to surface and then transport it back to Kristiansund.
If it is a compressor module, further work would be required before it could be removed, freeing it of hyr- docarbons and residual pressure before it is brought to surface.
The contents of the compression module would be displaced with MEG and then nitrogen, with the displaced
MEG removed to the scrubber module. The compression module would then be lifted over to the subsea parking frame, while the new module is lowered into position and commissioned.
Any residual hydrocarbons in the compression mod- ule would be diluted with nitrogen and then fared off via a hose connected to the SPI vessel process system topside, until the contents no longer pose an explosion
The Guys In Production The Guys In Production risk. During recovery through the water column, pressure in the compressor would be balanced by means of check
Are So Into It! Are So Into It!
valves, enabling the compressor to be at an ambient pres- sure before it is lifted on deck.
Highest capacity, minimum Highest capacity, minimum “Results of feasibility studies we’ve done show it is pos- sible to do this from monohul vessels,” Bjordal says. footprint, robust technology footprint, robust technology
If such a vessel was also used by Shell on Ormen Lange, and a clear cut: GEA Westfalia and a clear cut: GEA Westfalia project economics would improve further. Statoil and
Separator CrudeMaster – the Separator CrudeMaster – the
Shell say they are “cooperating” on the issue, but it is not best choice in oil treatment best choice in oil treatment yet clear what the solution will be.
for all offshore applications. for all offshore applications.
Shell, as Ormen Lange operator, has not yet concluded on the future infeld compression solution. In addition to subsea compression, a conventional tension leg platform is also an alternative for future infeld compression.
GEA Westfalia Separator Group GmbH GEA Westfalia Separator Group GmbH
In case the subsea solution is chosen for Ormen Lange,
Werner-Habig-Straße 1, 59302 Oelde, Germany Werner-Habig-Straße 1, 59302 Oelde, Germany
Owe says that Shell would need a new vessel in 2020, at
Phone: +49 2522 77-0, Fax: +49 2522 77-1778 Phone: +49 2522 77-0, Fax: +49 2522 77-1778 the earliest.
[email protected], www.gea.com [email protected], www.gea.com
Bjordal concludes: “We think having a new service for subsea process intervention is a key enabler to make this
Statoil subsea factory a success in the future.” engineering for a better world engineering for a better world oedigital.com
OI-215-1-005
OI-215-1-005 054_OE0813_Intervention-Asgard.indd 57 7/23/13 9:28 AM
AD_Crudemaster EN 105x275 - OI-215-1-005 - 2013-07_ok.indd 1 02.07.13 12:44 AD_Crudemaster EN 105x275 - OI-215-1-005 - 2013-07_ok.indd 1 02.07.13 12:44