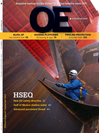
Page 100: of Offshore Engineer Magazine (Sep/Oct 2013)
Read this page in Pdf, Flash or Html5 edition of Sep/Oct 2013 Offshore Engineer Magazine
Articulated concrete mat protecting subsea pipeline. Photo: Submar.
and stabilization during the 1970s.
Rather than concrete, they were made
Pipelines of canvas bags flled with bituminous material and aggregates. This was not a formidable solution, as they would often split when submerged or would fail to take the pipeline shape due to their stiffness.
European companies were the frst to widely develop the technology for con- crete mats after environmental regula- tory agencies began cracking down on the use of sand or cement bags that were then-prevalent in stabilization, capping, and abandonment.
Mats produced in the early 1980s marked the frst usage of concrete to increase fexibility and versatility.
Initially made from concrete cured
Concrete mattresses in pre-made plastic pots that were interconnected with rope, this iteration was known as the link-lok mattress. offer more than just
Bituminous materials were prohibited by environmental regulatory agencies in the 1990s. Both the manufacturing pipeline protection technique and materials used needed further refnement to become the cost- effective, environmentally friendly
By Sarah Parker Musarra solution that the concrete mattress here are many methods used mats were a better solution than leav- presents today. to protect offshore pipelines: ing pipelines exposed,” said Monique Today, polypropylene rope is laid sand, grout or cement bags, Roberts, offshore division manager of into a form, with concrete poured over
T burying, concrete or cathode coating, Submar, a company that has produced it–no more plastic pots. The result? and trenching, to name a few. Most approximately 80,000 mats for the The wet-cast, 8-ft by 20-ft by 9-in- methods address ancillary issues like Gulf of Mexico over the last 20 years. thickarticulated concrete block mat separation, support, erosion, expansion “The situation was affecting two of that the pipeline industry knows today, of infrastructure, pipeline corrosion, Louisiana’s top industries [oil and gas; with 4000psi compressive strength. and ensuring that the pipeline infra- seafood].” Concrete density can range 1800-4800 structure itself is not detrimental to the Following four years of intense kg/cu m, depending on the amount environment surrounding it. battles, lobbying and at least two case of applied weight needed. To protect
Only one form of pipeline protection studies, the Louisiana Department the pipeline, the concrete is usually technology however, found itself in the of Wildlife and Fisheries enacted coated with a non-abrasive substance midst of a battle between the seafood General Permit 24 (GP24), in 2010, or pad that varies by manufacturer and industry of southeastern Louisiana, the and concrete mattresses continued product. oil and gas industry, and environmen- their industry reputation as one of the In the early 1990s, European com- tal agencies: concrete mattresses, also most reliable and cost-effective ways to panies began to license the technology commonly referred to as concrete mats. protect existing or expanding pipeline behind their mats. Submar, headquar-
While the mats were effective at infrastructure. tered in Houma, La., was one of the protecting and stabilizing pipelines original companies to receive this in the navigable waters off southeast- licensing in 1990 and they were the
History ern Louisiana, some fshermen were According to the ‘Concrete Mat Subsea frst to bring the mats to the Gulf of reporting that the mats were ensnar- Deployment Procedures’ published by Mexico.
ing the shrimp trawlers’ nets, greatly the International Marine Contractors The only major change made to reducing their harvest. Association (IMCA) in September today’s industry-standard size is that, “It took a long time and a lot of 2011, mattresses frst emerged as a at times, a 12-in. mat rather than the resources to convince everyone that method of subsea pipeline support industry-standard 9-in. thickness can
OE | September 2013 oedigital.com 102 102_OE0913_Pipelines1_Concrete.indd 102 8/17/13 6:39 PM