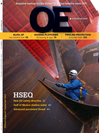
Page 115: of Offshore Engineer Magazine (Sep/Oct 2013)
Read this page in Pdf, Flash or Html5 edition of Sep/Oct 2013 Offshore Engineer Magazine
North Sea dynamic and two static umbilicals 550-tonne of steel replaced. high-pressure fare-knockout drum was (manufactured by DUCO Dynamic Neil Smith, offshore health, safety, also installed, replacing two vessels
Umbilicals, Newcastle), 11 fex- security, environment, and quality used previously, also improving the ible fowlines (from NOV Flexibles) (HSSEQ) specialist, Maersk, says: “Any footprint. and other subsea equipment,using vessel, through natural vessel move- A strong theme of the replacement
Skandi Arctic and Wellservicer ves- ments, is subject to stresses, fatigue, equipment was a greater ability to sels to install. Fugro provided survey and corrosion. You can deal with most capture, access and use data from the and ROV services from the Fugro of this offshore, but it is very challeng- process and marine systems.
Symphony, as well as ROV services ing, time consuming, and costly. When The Solar Turbines gas turbine for four Technip DSVs (dive support we had the opportunity to have the control systems were replaced with a vessels). Gryphon Alpha in the yard we were Turbotronic 4 system, including new
Maersk used 22 diverless hull con- able to do a lot of that work.” programmable logic controllers (PLCs), nectors, supplied by FES International, The vessel’s three Hydralift hydrau- enabling more information about to install the risers, which was trialed lic cranes were removed and refur- performance to be accessed, including onshore before the offshore campaign. bished with upgrades addressing obso- analyzing alarms and ability to access
In total, about 39km of fexible lescence issues. New loading alarms data from a remote terminal at the fowlines, umbilicals and risers were and boom-tip cameras were also ftted. bridge. installed, as well as 3000tonne of In addition, new bumper bars were The Provox process control system structures, the mid-water arches and installed to protect high-risk areas dur- (PCS), which was becoming harder 21 wells hooked up, utilizing 703 ing lifting operations. to maintain due to obsolescence, was vessel days. A new, taller, inert gas tower, includ- replaced with an Emerson Delta-V ing high velocity vent valves, was system. This meant increased access installed, standing 24m above the pro- to data for onshore teams, for moni-
FPSP Gryphon Alpha
The Gryphon Alpha arrived in dry duction deck, to increase its distance toring and reviewing trends. Due to a dock at Damen Shiprepair Rotterdam from the vessel. Lay down areas were change from switches to transmitters, (Schiedam) on June 27, 2011. expanded and improved, by replacing the application of plant inhibits will
Superfcial cracks, not identifed a metering skid with a new, smaller, also be reduced through improved offshore were found, enabling a more multi-phase system, and removing an monitoring. thorough overhaul than could have old dehydration unit and produced One of the biggest pieces of work been achieved water systems. was the installation of a new second- offshore, with A new stage separator, says Marc McAndrew,
Gryphon asset process engineer.
The existing second-stage separa- tor had a design pressure of 3.1 Bar(g) but the upstream frst stage and test separator systems wererated to 12.9
Bar(g) and were operating in the 9-10
Bar(g) range. A fully rated replacement vessel, including new pressure safety valves, was installed at 12.9 Bar(g) design pressure.
This was supplemented by a new
HIPPS (high-integrity pressure protec- tion system), with two, 16in. Mokveld valves on the production header, two 6in. Mokveld valves on the test header, and an intelligent logic solver from Yokogawa. This was the result of analysis, which highlighted a potential to overpressure the frst stage and test separator, due to de-packing of fow lines potentially at gas lift pressure.
In addition, a nucleonic density profler was added to the second-stage separator, allowing increased visibility
Gryphon Alpha out of the drydock at Damen Shiprepair Rotterdam (Schiedam). Photo: Maersk Oil North Sea UK oedigital.com September 2013 | OE 117 000_OE1013_geofocus1-gryphon.indd 117 8/17/13 5:33 PM