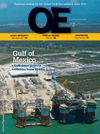
Page 54: of Offshore Engineer Magazine (Oct/Nov 2013)
Read this page in Pdf, Flash or Html5 edition of Oct/Nov 2013 Offshore Engineer Magazine
subsea equipment. High-pressure felds, particularly, dedicated test facility focusing on deep
Valves manufacturer Bel Valves, at St have driven change, she says, with water, and HPHT. The next step, says
Peters, Newcastle, is part of the group a need for high-integrity, pressure- Ennis, is moving in to even higher bidding for the hyperbaric facilities protection systems (HIPPS). Bel Valves pressures, such as 20,000psi pressure
EPIC and is another company expanding. has worked closely with BP in this area, through the pipeline.
Alison Ennis, Bel Valves marketing including on the development of a sub- “We are starting to look at limit of manager, says the company was early sea HIPPS for the Shah Deniz II project. tolerance of metal itself,” she says. to focus on critical subsea applications, To meet demand, the company, “Pressures have continued to increase, focusing on high-pressure high-tem- owned by British Engines, plans to which has meant products have got perature (HPHT), hydrogen sulfde, increase its premises by 30%, by relo- bigger and they cannot ft in the mani- and deepwater, as well as developing cating sister company hydraulics frm fold. Then if they can get it in, they all electric subsea systems, including Rotary Power, freeing-up 12,500sq m. can’t get it out because it is heavy. We single actuators for valves. This will enable it to create a are looking at redesigns and alternative design metallurgy.”
Northeast England is still also home to large-scale fabrication, although not on the same scale as in the past. This summer, OGN, based at the Hadrian
Yard, completed its frst project,
Apache’s Forties Alpha satellite plat- form. It is now working on the Monarb (Montrose/Arbroath) platform jacket for Talisman Sinopec Energy UK.
OGN wants to move into industrial- scale production of jacket-based foundations for the offshore wind sector. However, the market has yet to fully emerge for offshore wind jackets and a new manufacturing facility to do the work requires US$100 million investment.
OGN, which can handle facilities weighing up to 13,000-tonne, is look- ing to work outside the North Sea, and looking to smaller work it could do at its Lowestoft yard, which has until now been dormant, says the frm’s Carl
Jepson.
Another fabricator, TAG Energy, has made the move into the renewables market. The company opened at the 42-acre, former Furness and Swan
Hunter shipyard on the River Tees in 2007, in order to build a topside for a deepwater semisubmersible.
The project was dropped by the client and TAG decided to refocus on renewables, raising £20 million in grants and equity funding to develop new facilities, with further £15 million invested since then.
Last year, TAG became the frst com- pany in the UK to start manufacturing offshore wind turbine monopiles and transition pieces, with a 24/7 opera- tional linear manufacturing line.
Alex Dawson, CEO at TAG, would like the site to be producing 60-100 monopiles and transition pieces per
OE | October 2013 oedigital.com 56 052_OE1013_EPIC4-newcastle.indd 56 9/29/13 10:03 PM