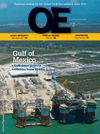
Page 61: of Offshore Engineer Magazine (Oct/Nov 2013)
Read this page in Pdf, Flash or Html5 edition of Oct/Nov 2013 Offshore Engineer Magazine
eliminates the risk of taking a produc-
Subsea ing well out of production.
Shorter time to frst production
While the period of time necessary to design, fabricate, install, and commis- sion a well protector tripod platform will vary greatly around the world, 12-18 months from contract place- ment to commissioning is a typical duration for these activities. In some cases, the wells can be pre-drilled; however, it isn’t unusual to wait for the platform to be installed before drilling the wells to minimize pre-investment.
Producing a stranded reserve through a new wellhead platform potentially means production won’t start for 18-24
FMC Technologies months after project sanction.
JXT-3 shallow water
With no pre-investment, a shallow subsea tree is confgured water subsea system can be installed for a single well tie-back.
and commissioned in as little as 9-12 months after project sanction. With tie-back using direct hydraulic con- manifold and control system distribu- minimal pre-investment, production trols is the simplest form of subsea tion skid. A dual or single fowline can start as soon as six months after tie-back. Direct hydraulic controls are transports production from all wells to project sanction. FMC Technologies an excellent, safe means of controlling the processing platform, with subsea has implemented a stocking plan for the production tree for tie-backs to chokes mounted on the trees to balance long-lead equipment to reduce delivery 8km (5mi.). Most applications include production fowing pressure and rates times even further. With minimal pre- electrical conductors in the umbilical from each well in the fowline. Jackups investment, an operator can drill and for instrumentation mounted on the aren’t able to easily and quickly move complete a well with a single mobiliza- tree. Chemical injection to prevent or a few hundred meters to a new well, so tion of the jackup drilling rig. remediate hydrate and wax issues is drilling templates are used to cluster accomplished via one or more chemi- wells into drill centers under the rig’s cal tubes in the control umbilical. cantilever deck to avoid moving the
Reduced installation costs
Installing a new wellhead structure Multiple well developments also rig to a different location for each well. entails mobilizing a derrick barge hold the potential to achieve consider- Care must be taken that the center to the location for the installation able cost savings using shallow water point of each well is within the work- work. Within the past year, IHS subsea systems, though it is impera- ing envelope of the cantilevered drill-
Petrodata reported the global average tive to keep the seabed architecture ing and Texas decks of the proposed rate for a derrick barge is the range synergistic with jackup rig operations. drilling rig. Two-, three-, and four-well of US$300,000 to $350,000 per day. When developing the seabed architec- templates are quite common; some rig
Shallow water subsea production ture, consideration must be given to cantilever deck windows and template systems are designed to be installed the rigs being considered for drilling. layouts can accommodate as many as from the drilling rig, thus the cost of Shallow water seabed architecture six wells.
the derrick barge is eliminated from differs signifcantly from its deep In addition to wellhead locations the capex. This is also true for decom- water brethren as the shallow water and geometry, another important con- missioning costs. The shallow water seabed architecture must consider sideration is the method of connecting subsea system components are recov- the time necessary to move a jackup fowlines and pipelines. The common ered by the drilling rig when the well from one location to another. In felds default practice for subsea systems is is plugged and abandoned, eliminating drilled with a foating rig, the rig can to use diverless hydraulic connectors, the costs of the derrick barge to salvage easily and quickly move a few hun- such as FMC Technologies’ U-Con con- the wellhead platform. dred meters to keep the well’s surface nection system, for connecting fow- location directly above the bottom lines, jumpers, and spools to the sub- hole location. As a result, the favored sea hardware. For the shallow water
Field architecture
To achieve maximum cost beneft of seabed layout is a central manifold system discussed, saturation diving using a shallow water subsea produc- with production trees and injection techniques allow these connections to tion system, the seabed architecture trees spaced around the manifold. be made using conventional pipeline must be planned specifcally for Flowline jumpers and umbilical fanges; swivel fanges and mis-align shallow water felds. A single well fying leads connect the tree to the ball fanges; studs; and nuts installed oedigital.com October 2013 | OE 63 062_OE1013_subsea2.indd 63 9/29/13 7:35 PM