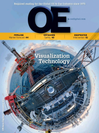
Page 29: of Offshore Engineer Magazine (Nov/Dec 2013)
Read this page in Pdf, Flash or Html5 edition of Nov/Dec 2013 Offshore Engineer Magazine
damaged or stuck casing by enabling Through morphing the tieback casing plan for drilling deeper; and provides
Drilling operators to cut the original stuck or into the Meta tieback receptacle, an ISO fexibility of space out.
damaged casing at the required point, 14310 VO gas tight certifed metal-to-
Redefning well integrity and deploy the reconnect solution over metal connection is established with no the existing casing, and reconnecting it to reliance on elastomers. The durability These examples focus on structural and new casing with a connection capable of of the metal-to-metal seal enables it to casing integrity. Metalmorphology is withstanding over 1,000,000 lbs of axial operate at pressures of up to 30,000 psi, also playing a role further along the well loading, and providing a metal-to-metal and temperatures of more than 160°C. lifecycle, allowing for the proactive plan-
V0 gas-tight seal. An axial load capacity of 1,700,000 lbs ning of zonal and barrier integrity as well
It has been used in the southern North makes it suitable for deepwater environ- as restoring well integrity and enabling
Sea, where an operator was faced with ments, such as the Gulf of Mexico, with operators to isolate selected zones during a 9-5/8" leaking casing string and had the axial loading bearing capabilities production.
lost signifcant rig time attempting to allowing for deeper drilling. Metalmorphology is proving how well regain integrity, with the use of swellable Additional benefts are reduced rig integrity can be planned and how pre- technology being unsuccessful. Costs of time for the landing and spacing out of existing technology limitations can be the project were escalating and a solution the casing string. overcome, reducing risk, protecting and had to be implemented within a small A series of Meta tieback systems are maximizing future production. operating window to ensure integrity was due to be installed by Shell in a deepwa- regained. ter Gulf of Mexico feld. The operating Richard Craig, vice
Meta’s Metalmorphology-based temperature will be 120°C and, once president of business reconnection system was deployed and the tieback is installed, the deployment development at Meta, resulted in the placement of a metal-to- depth 10,000 ft. Hydrostatic pressure at has 25 years’ metal connection of the existing 9 5/8" this depth will be 3750-5800 psi, depend- experience in the casing string to the surface. ing on fuid in the well. offshore and onshore
The operation allowed the operator to
Through the incorporation of the oil and gas sector, continue with their well plan without liner tieback into its well architecture, primarily within the the need for intervention work and the
Shell will ensure the well architecture drilling sector. Previous roles include pulling of the casing, leading to cost remains fully compliant with current business development manager at savings of nearly US$4 million. The regulations; overcomes limited IDs in Enventure International and technical well now has a reinstated life of well casing strings to achieve high load bear- sales director at Global Drilling Supplies. gas tight seal qualifed to more than ing capabilities; allows asset teams to He also spent 16 years at Noble Drilling.
5000 psi and a casing capable of car- rying more than 600,000 lbs in tension Inside the Meta liner tieback.
Photo: Meta.
and compression.
Meeting Regulatory Demands in the Gulf of Mexico
In the Gulf of Mexico BOEMRE/BSEE requests additional information on well planning activities in the form of a new worst-case discharge criteria, particu- larly applicable in deepwater wells. All assumptions made regarding well design, estimated fow rates, the maximum dura- tion of potential uncontrolled fow and the total volume must all be considered.
This has made it necessary for operators to alter their well designs and strengthen well architectures—particu- larly at the earlier well lifecycle stage—to adhere to these regulations.
While there are a number of liner tieback solutions on the market, many are dependent on elastomeric elements.
Elastomers come with a number of reli- ability issues relating to their sealing capabilities and duration and potential internal diameter (ID) reductions.
Meta has developed a liner tieback solution to enable operators to dem- onstrate and often exceed legislative compliance. oedigital.com November 2013 | OE 31 000_OE1113_D&C1-Meta.indd 31 10/28/13 1:28 AM