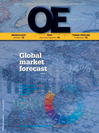
Page 38: of Offshore Engineer Magazine (Jan/Feb 2014)
Read this page in Pdf, Flash or Html5 edition of Jan/Feb 2014 Offshore Engineer Magazine
Drilling
Gaining new access to old wells
By Jimmy Land and David Moran, not impacted by the dogleg
Table 1: Modeled versus across the whipstock. A
Schlumberger actual wellbore trajectory drillstring analysis program Top of milled Depth,
Inclination Azimuth n an age of increasingly hard-to-tap models the sidetrack and window ft resources and high demand, operators provides real-time analysis of
WhipSim software
I are continually searching for reliable, the modeled parameters. 1,444 7.6 201.3 model
In the North Sea project, cost-effective ways to extend produc-
Gyro measured1,444 7.76 201.15
Schlumberger selected the tion and improve recovery in mature or whipstock technology for a damaged wells. A cased hole whipstock
Bottom of rathole customer wanting to perform system that uses dynamic modeling soft- an ef? cient, cost-effective ware to engineer a wellbore exit design,
WhipSim software 1,485 9.8 194.4 model slot recovery operation on a is providing new access to old wells that well that had been drilled in might otherwise be abandoned.
Gyro measured1,488 10.75 191.02 1974 and recently plugged
A North Sea operator used the whip- and abandoned because of damage to the stock system to successfully sidetrack to mill clean, full-gauge windows for existing completion and casings. Such an an aging, abandoned well and perform a access to wells with high-grade steel and endeavor is typically costly and requires slot recovery that created access to a new chrome casings, and in formations with several days of rig time. wellbore. The system set a mechanically uncon? ned compressive strengths of anchored whipstock in the existing cas- more than 40,000 psi. The technology, The objective was to set the whipstock ing, milled a full-gauge 18.5-in. window which can be con? gured to provide fast, in the original 20-in. casing, mill a clean, and set the world’s largest tight-tolerance high-quality windows and sidetracks for full-gauge 18 ½-in. window to provide liner in the 20-in. casing, saving the any application, is enhanced with the use access for the new wellbore and then run operator ? ve days of rig time. of sophisticated casing exit simulation a large, 17-in. liner through a casing exit
The Schlumberger TrackMaster CH software that helps ensure subsequent with the dogleg optimized for the com- cased hole whipstock system is designed drilling and completions strings are pletion string. Pre-job analysis, modeling and planning were integral to optimizing the design of an operation that would
Fig. 1: Casing exit simulation – window geometry deliver a successful outcome.
-300 -300-300
Inner casing wall
Planning the Installation
Outer casing wall -200 Rathole
During the planning stage, simulations -200-200 provided realistic predictions of how -100 each bottomhole assembly (BHA) would -100 perform, while calculations were made to 0 indicate the stresses of all the components 0 as they passed through the window. The 100
WhipSim* whipstock simulation software 100 was used to ensure the tight-tolerance 200 200 liner could be installed with the large-size whipstock assembly and window. 300 300
This was accomplished by modeling
Distance from top of whip, in.
the milling operation and the geometry 400 400 20 of the milled window, and by testing 10 500 the pass-through assemblies for the 0 500 completed window. An advanced mill -10 -10 0 design platform validated the milling 10 600 20 30 -20 20 -30 -10 10 30 00 -20 20 -30 -10 10 30 40 string design and operating procedures.
Distance from borehole, in.
The Runner drillstring analysis program 3D view modeled shear setting operations, jar
By calculating DLS for the casing exit, the WhipSim software helped ensure that placement, dogleg severity (DLS) and completion strings were not a