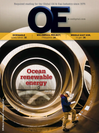
Page 22: of Offshore Engineer Magazine (Feb/Mar 2014)
Read this page in Pdf, Flash or Html5 edition of Feb/Mar 2014 Offshore Engineer Magazine
OCEAN RENEWABLE ENERGY
Inter-array cable laying
IHC Merwede aims to resolve some of the challenges of offshore wind cable installation, specifcally burying inter-array cables, with its Hi-Traq subsea trenching vehicle, developed by its business unit, IHC Engineering Business.
Chris Jones, product manager, subsea vehicles, says: “We started with a clean sheet and looked at all the environmental impacts, cost, schedule and technical issues around burying inter-array cables. The shallow water (20-50m typically) makes it a completely different environment from deeper water oil
Left — Technip’s pull-in module, being lifted onto a transition and gas operations. Wind farms are in shallow water to limit piece on the Lincs Wind Farm, ofshore Lincolnshire. Right — A foundation costs, which means a stronger seabed and wave visualization of Technip’s pull-in module. Images courtesy of Technip. interaction, which in turn infuences current and activity at the deck foor not being designed to take loads associated with seabed, such as shifting sand ripples and mega ripples. This equipment. infuences the type of vehicle needed.” cable pull-in “Traditionally these issues have been overcome by utilizing In these environments, free-swimming ROVs, or using cutting a simple steel Tripod A-frame, installed on the turbine fange, or jetting technology to trench, may not be suitable. which is the only area strong enough to take the forces associated The smallest Hi-Traq unit, equipped with pressure jetting with the cable installation,” Kearney says. However, set up takes equipment, has been designed to weigh 15-tonne in the water up to three hours, is weather sensitive and the installation pro- (25-tonne in the air, compared to 40-50-tonne for existing cess poses risks to crew safety, with potential for signifcant harm tracked trenchers). This is estimated to be the minimum weight if the cable, under high tension, breaks, and operational risk. required to keep it on the seabed in 4-6 knot currents. It will be
Technip’s solution is a 5.9-tonne pull-in module (PIM), con- rated to 1000m water depth to perform cross-market operations. sisting of a tripod structure (to install in one lift using self-align- The aim is for it to be easy to mobilize, and to have a ing guide pins onto the turbine fange on the transition piece, minimum footprint, to enable its use on smaller vessels. A with a small integrated winch) and dedicated power supply, larger version, incorporating a mechanical cutter, could have a able to run for more than 18 hours. A secondary independent submerged effective weight of 30-tonne, with potential for an power supply could power lighting. It also has two large storage 80-tonne version to be built, which could operate in the oil and units, with about 100kg of equipment often required on a pull, gas market. and multiple hang-off points around the hand rails, to enable The system, developed with regional development fund fund- equipment to be loaded before transfer to the transition piece. ing, is based on a four-track undercarriage design with bogie
The PIM eradicates any effects of vessel motion on winch arrangements. Each track has independent suspension, maximiz- wires during pull-in, currently performed from a vessel, and ing seabed traction capability, which means it can turn in a 10m allows the winch operator to be located at the work site. circle instead of a 50m circle on previous vehicles. It also has the
In addition, Technip suggests certifed attachment points be capacity to ‘crab,’ for working on slopes or uneven surfaces. added all over the structure to give personnel clip-on points The shallow water environment means it can cope with is working close to an exposed edge, as well as hand rails and burying the laid slack required for the pull-in operation. While equipment guards on the upper work platform. a jetting ROV could do this, it cannot do it all the time, depend-
The system has been deployed on the Lincolnshire Offshore ing on the current. Hi-Traq can also reverse up to foundations,
Wind Farm, off England, with an average 2.5hr cable pull-in then track away.
time, compared to 6.5hr on the Thanet Offshore Wind Farm, A demonstration vehicle was completed earlier this year,
Kearney says. with testing and validation scheduled for Q1 2014.
IHC Merwede’s Hi-Traq inter-array cable laying concept. Image courtesy of
IHC Merwede.
February 2014 | OE oedigital.com 24 022_OE0214_ Cover3_Wind Cable.indd 24 1/21/14 3:55 PM