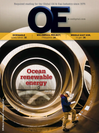
Page 31: of Offshore Engineer Magazine (Feb/Mar 2014)
Read this page in Pdf, Flash or Html5 edition of Feb/Mar 2014 Offshore Engineer Magazine
simple workover of an offshore well in set plugs in the well to keep the well sooner than a conventional workover.
Drilling the Middle East might cost upwards of isolated, after which the tree was pulled This helped to signifcantly lower the
US$6 million, according to estimates and a spool piece containing a hanger risk of formation damage or lost produc- from the operator. profle was installed. The tree was then tion that may result from extended well
Weatherford collaborated with the reinstalled and after the wellhead was downtime. The installation was also operator to develop an alternative pro- pressure tested, the wireline crew went conducted at a fraction of the price of cess—an intervention that would restore back in and pulled the plugs. a full workover, coming in at less than functionality to the SCSSV by retroftting Another trip downhole was conducted 10% of the estimated US$6 million a new control line and inserting a new to lock open the existing tubing-retriev- workover cost. valve within the existing well architec- able safety valve, after which a new The installation in the frst well suc- ture. The operator required the interven- subsurface safety valve was deployed cessfully proved the viability of this tion to be performed without killing the and landed inside the previous valve. technology, and it has been running well, pulling the tubing or incurring the Once the new valve was set, the capillary without issue since May 2013. The time delays and costs that commonly control line was run down the center of operator was pleased with the ease of come with a major workover. the tubing to a pod on the valve. installation of the system, the sig-
A weighted and centralized stinger nifcantly lower rig time and the fewer
A Renaissance in well revival placed at the end of the capillary string number of trips required. The new
Upon review of the well parameters was used to join the capillary to a mat- SCSSV system also eliminated the need and intervention requirements, the ing connection on the valve. This was for a storm choke, which was prone to operator decided to deploy Weatherford’s a wet-connect assembly, which was repeated tripping and caused production
Renaissance WDCL system, a wireline- hydraulically locked in place by apply- interruptions.
The operator was able to restore retreivable subsurface safety valve that ing pressure to the capillary string. The the well to full production once the allows both the control line and the wet connect contains unique design fea-
SCSSV was fully operational, and safety valve to be replaced in a straight- tures, including the ability to be mated now plans to install this solution on a forward retroft procedure. and unmated should the capillary need number of additional wells suffering
The system has a modifed pack- to be removed, and dual-back check from the same control line blockage ing mandrel and wet connection, and valves that prevent backfow through issues. These issues are not unique to a valve-and-lock assembly that can be the capillary line as an additional safety this operator, or to the Middle East; installed in an existing tubing-mounted feature.
Weatherford is actively working with safety valve or safety-valve landing nip- The top end of the capillary was then other operators to install similar SCSSV ple. A capillary line is then run from the landed into the new spool piece below systems in offshore wells throughout surface inside the tubing and connected the tree through a specially designed, the world. to the valve to provide control. 4-in. control-line hanger. A Type-H
The retroft process for this offshore profle was provided above the hanger to The Renaissance WDCL was installed well was performed from a jackup rig, allow for the installation of a backpres- without incident, allowing the operator and began by modifying the wellhead to sure valve, which would be required to to bring the well back to full production provide the correct profle for the capil- secure the well during future wellhead quickly, while adhering to offshore safety
Workover-free option restores lary hanger and gain access for the new maintenance. regulations in the region. capillary control line. A wireline crew The entire installation took only two A new spool piece was placed below days of rig time, allowing the well to the lower master valve on the wellhead. safety valve functionality be brought back into production much The spool piece was custom-built with a profle to lock the control line hanger in
However, SCSSVs are prone to mal- place, and polished bores for the seals. function, which is commonly caused by piston failures, leaks within the valve body or some type of control line failure such as crushing, leaking or blocking by an obstruction. Such a control line failure occurred in the offshore Middle East well, which forced the valve closed and shut in production.
The conventional remediation method calls for bringing in a workover rig to pull the tubing, replace the blocked control line and then redeploy down- hole. While this option is relatively cost-effective and easy to implement in
Picture of the WDCL an onshore well, the logistics, cost and
Subsurface Safety Valve in the closed position complexity of performing a workover (fapper shown in gold), the blue highlights the fow path of offshore make this a time-consuming and hydraulic fuid to function the valve.
expensive operation. Even a relatively
Image courtesy of Weatherford.
oedigital.com February 2014 | OE 33 032_OE0214_DC1.indd 33 1/20/14 11:54 PM