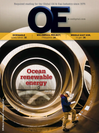
Page 33: of Offshore Engineer Magazine (Feb/Mar 2014)
Read this page in Pdf, Flash or Html5 edition of Feb/Mar 2014 Offshore Engineer Magazine
in the footings, and during the positioning Barge Master motion-compensated
EPIC of a bridge between the two platforms. platform lifting system will be ? tted on
Ndeavor’s sister vessel, Ndurance, is the aft of Ndeavor. It will then sail out to the designated cable layer, and is being location. Once on site, the bridge will be ? tted with a 5000-tonne turntable. held still by the Barge Master so it can
These vessels had to be as versatile as be lifted off safely by two temporarily possible to ful? ll the requirements of the installed lifting arrangements. client. Ndeavor had to have DP2 capabil- This bridge, which is around 220-250 ity and we felt the best solution was to ? t tonnes, can be lifted safely from the mov- the vessel with both excavation and rock ing vessel by the Barge Master system, installation equipment. which provides a very stable platform.
The ? rst phase of the work offshore The use of the Barge Master is a world will be preparing the seabed for the ? rst, using largely proven technology but installation of the DCP, which will in an innovative way.
involve excavating down to various The integrated approach has many depths. bene? ts for the client. We can handle all
Ndeavor can handle the entire scope of the work in-house: rock installation, in the ? rst phase. The vessel will remove earth moving, tow out, installation of the top layer of carbonate sand, and, after the new platform, ballasting of the legs, excavation, use engineered rock to back install the iron ore to give stability and ? ll to an elevation of -42.73m Lowest the bridge between the new and existing
Astronomical Tide (LAT). The removed platforms.
sand will be taken to a designated loca- Our client does not have to deal with tion alongside the platform. interface issues. Usually the seabed work
A trial seabed preparation pad will would be completed, then we would then be constructed and validated south hand over to the client, and then the cli- platform and the dry gas transported of the proposed DCP location before ent hands over to a second contractor for via a 504km-long (313mi) 24in. export construction of four seabed preparation the rock installation. Also, because one pipeline to Batangas port for further pads on the back? lled surface, to a target multipurpose vessel is doing many tasks, processing. LAT -41.73m. the client has to approve only this vessel.
The project is one of the ? rst in which Surveys of each phase of the work, Shell accepted Boskalis’ own safety the expertise of Boskalis and SMIT, including pre-excavation, post-excava- program No Injuries, No Accidents acquired by Royal Boskalis in 2010, have tion, pre-back? ll, post-back? ll, pre-pad (NINA), on the project.
The Malampaya project is the second been brought together in an integrated installation, post-pad installation surveys assignment in a row that Boskalis Offshore package. and progress surveys during the execu-
The phases of the project. is executing in the Far East for Shell.
Boskalis was awarded the contract in tion of each phase.
Image courtesy of Boskalis O