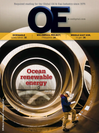
Page 38: of Offshore Engineer Magazine (Feb/Mar 2014)
Read this page in Pdf, Flash or Html5 edition of Feb/Mar 2014 Offshore Engineer Magazine
Subsea
Riserless drilling
A dual drillstring
Image courtesy of Reelwell makes a comeback
When one thinks of “retro,” a
Out with the old…
Administration (NOAA) says about
For decades, risers have been a standard 63% of the 1.6 million b/d of oil pro- number of things may come in drilling operations, but as companies duced in the Gulf of Mexico come from to mind – old clothes, vintage wade further offshore, traditional drilling ft). depths lower than 1000m (3280 methods will pose greater ? nancial and Riserless systems are not foolproof. furniture, maybe even a classic technical dif? culties. Several studies have pointed out ? aws, car – but in the world of subsea
Risers are more cumbersome to use including dif? culities in cleaning a top well operations, there are three in deeper waters; the money and labor hole, potential tubular failures, and needed to build a riser capable of han- increased torque and drag. There’s the words that best ? t: dling the stresses drilling beyond 5000- potential for oil or natural gas to seep
Riserless drilling systems 6000ft, as well as the platform required through the tophole and into seawater, to hold it, are extensive. Large risers also causing environmental problems and increase the risk something could go potentially endangering the rigs or drill
By Stephen Whit? eld wrong with equipment. A malfunctioning ships. Gas bubbles building underneath iserless drilling systems are riser in a deepwater well could signi? - a rig could trigger an explosion, or in the based on schemes that have been cantly impact the environment. case of a drillship, cause the density to
R around for the better part of 50 Watkins patented the ? rst riserless drop enough to make the ship sink. years. They’ve always been on the back- system in 1969, in part to balance subsea In a 2011 study examining drill burners of companies looking to increase well pressures and make it easier for the casings in riserless topholes, Robello the ef? ciency of drilling operations and drill pipe to re-enter the drilling hole. Samuel of Halliburton and John reduce the heavy costs that come with At the time most offshore rigs drilled Gradishar of Shell pointed out buckling them. But the technology was not there to relatively shallow waters, and although failures with some riserless systems, in make those schemes a reality. companies continued exploring deeper which poor hold conditions led the cas-
In the last decade, however, as technol- water, any problems could be solved by ing to compress above the mud line. In ogy has caught up to theory, riserless increasing the size of the marine riser that same study, they proposed a “new drilling has become an attractive alterna- and the subsea wellhead. modeling approach” to help deal with
Today, it’s a different story. The US tive to standard methods. the torque and drag issues.
National Oceanic and Atmospheric
But regardless of the potential pitfalls,
February 2014 | OE oedigital.com 40 040_OE0214_Subsea2_RiserlessDrilling.indd 40 1/20/14 10:30 PM