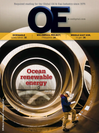
Page 56: of Offshore Engineer Magazine (Feb/Mar 2014)
Read this page in Pdf, Flash or Html5 edition of Feb/Mar 2014 Offshore Engineer Magazine
the control system. “Pumps have not changed much over the years, but instrumentation and controls are much more advanced now,”
Martin says. “We used to have a wall of
Vessels the control room covered with a process fow diagram, switches and a panel of hundreds of valves that needed three people to operate. Today, controls look like something out of a science fction movie. They are remotely operated by a small number of people in the control room via touches screens, and can even be operated from onshore.”
The entire stimulation system is controlled from inside the control room.
Within the vessel’s monitoring system is a data acquisition system, which gathers data and transmits it to the data analysis software, which supports remote satellite monitoring, from onshore. A battery- powered wireless data acquisition skid can be positioned on a platform or rig The Blue Orca’s touch screen control room. Photo courtesy Elaine Maslin.
to transmit data back to the vessel using
Clark says. “If anything goes down, there meter, with radioactive densimeters to wireless LAN communications.
The automated systems eliminate the will always be at least one back up,” he measure the blended acid concentration.
need for staff to work in hazardous envi- says. “We should never have to stop a The sand proportioning system is ronments around the rotating or high-pres- job because we were not able to switch also computer-controlled and fully pre- sure equipment under normal operations. pump.” The blending and mixing process programmable. Blender tubs are directly systems have full redundancy, he says, under the silos to simplify the sand The marine systems, have been built and stimulation and power plant systems delivery process. Pneumatic conveying to be able to operate in the North Sea’s run independently from the marine delivers proppant from below deck stor- harsh conditions, including a 10m swell, power systems. age to the above deck proppant silo, and or 40knot wind. It has a drop-down,
The blending system allows for acid, it is possible to return proppant back to electrically powered azimuth thruster, water and additives to be blended, the below deck tanks. able to rotate 360° for station keeping. without going through an open tub, creat- The gel blending plant on the vessel The marine power systems are sepa- ing a closed, automated system, with a uses dry-on-the-fy technology, which rated from the treatment and pumping maximum delivery rate of 80 bbl/min, means oil-based slurried polymer con- systems. to minimize potential spills or releasing centrates are not needed. This system The vessel has enclosed external walk- hazardous fumes. It will be able to work uses a full automated system, to control ways, and single-man cabins. The vessel in automated batch mode, automated the addition of dry guar, or other gelling works with two crews, for 24-hour opera- continuous batch mode, and continuous agents, into the fuid stream. High-energy tion. Support crews also arrive at the rig mix, all through a pre-programmed com- mixers shear the polymers for hydration. or platform before the vessel, so there is puter control system, which also continu- The viscocity of the gel is monitored no need to transfer personnel from the ously monitors the rates and adjusts them inside the vessel’s onboard laboratory, vessel to the rig. accordingly. Concentrations are moni- with real-time pH, temperature and The vessel undertook its frst job for tored using a Coriolis-effect mass fow viscosity data recorded and displayed via a North Sea operator in December, to improve the injection profle of a water 180,000-gallon raw acid capacity. Proppant change until 2010. injector well, which supports reservoir storage capacity was more than 2 million lb. Shortly after the left for India,
Vestfonn pressure. The job consisted of three
The ’s maximum pumping pres- a new company, StimWell Services, was
Skandi Fjord stages of a viscosifed 15% HCL with two sure was 15,000-psi, supported by 10,400 launched out of Great Yarmouth, the stages of Baker Hughes’ diverter system, hydraulic hp. ’s former base. StimWell launched
Vestfonn
Enhanced Acid System. Pumping rates
Apart from the short-lived introduction of the 86m-long , a conversion,
Island Patriot were 4-12 bbl/min. Pressures were 3000- the , in 1993 (it left the in 2010.
Western Renaissance 4000 psi, using about 1200 HHP.
North Sea in 1994, and was converted into The , which is owned by Island Patriot
A step rate test (SRT) was performed a pipelay vessel after working in the Gulf of Island Ofshore and managed by Island before and after the treatment. The
Mexico from 1994-1995), the departure of Ofshore Management, started a four-
SRT after treatment showed much less the to India in 2007, and the occa- year contract with BP, primarily for use on
Vestfonn surface pressure, compared to before the sional use of modular stimulation packages the Valhall feld, in 2010. Island Ofshore treatment.
on supply or support vessels, the stimula- is a 50:50 joint venture between Edison
The vessel was on location for about 24 tion vessel feet in the North Sea saw little Chouest and Ulstein Group. • hours and saw zero HSE incidents.
February 2014 | OE oedigital.com 58 056_OE0214_vessels1.indd 58 1/20/14 9:41 PM