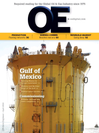
Page 49: of Offshore Engineer Magazine (Apr/May 2014)
Read this page in Pdf, Flash or Html5 edition of Apr/May 2014 Offshore Engineer Magazine
Tubular Bells had received a letter of a well head on the seabed, instead of a the system, as opposed to the multiple system, the vertical blocks were rotated award from Hess. In a news release riser. It is a more complex design than a interfaces one would get in dealing with to a horizontal position once completed,
EPIC issued at the time, the company said it conventional dry tree system – since well multiple companies. after which they were lifted and set into would handle “production handling, access is not at the surface, it is harder to Another key to reducing the construc- the graving dock for incorporation into export pipeline, oil and gas gathering and access during intervention – but it allows tion time was choosing to build in the the hull.
gas processing services” for the proj- for a lower-cost hull and does not restrict US. It is no secret that Gulfstar is the frst “Gulfstar provides a complete ‘foat- ect; in other words, it would design the vessel fexibility to the spar. spar-based FPS whose major components ing production system to market clearing engine that made the whole thing work. Gulfstar’s topside has a maximum oper- were built in America – the topsides point’ solution for producers in the Gulf
Costing an estimated US$2.3 billion, ating payload of 8600 short tons, three were constructed by Gulf Island Marine for their oil, gas and liquids produc-
Tubular Bells was designed in the ever- two-phase production separators, and a Fabrication in Houma, Louisiana, while tion, designed specifcally to maximize popular “hub and spoke” delivery model. one-phase test separator, each of which can the hull was constructed at Gulf Island their net present value and minimize
Under this layout, Gulfstar is the hub, handle 30,000 bbl of liquid per day (blp/d). Fabricators in Aransas Pass, Texas. In all, risk,” said Mark Cizek, Williams’ the center to which all resources will Its three T60 power generators each run about 90% of the materials for Gulfstar Gulfstar Project Director. “The ‘design eventually go. It will be connected to two on a dual fuel confguration and features came from the US. one, build many’ construction concept subsea drill centers, which in turn will a waste heat recovery system. allows for standardized design be connected to three subsea production It is built to last 25 years and options and enhanced safety wells and two water injection wells. house up to 50 people at any and reliability of each unit.
Gulfstar’s platform was installed at given time. It has a single-piece The repeatable concept also a depth of 4300ft. Its core module has lift that can handle up to 6600 increases speed to market.” the capacity to produce anywhere from short tons.
What’s next?
60,000 to 90,000 bo/d, but Hull expects The hull can reach a depth of to yield 120 billion bbl from Tubular 8500ft. Its outside diameter is In addition to anchor com-
Bells, with peak production estimates 85ft, and it measures 60ft from mitments from Tubular Bells coming at 40,000 to 45,000 boe/d. the top deck to the waterline. owners, Gulfstar executed
It has two pull tubes that can agreements in January with
What is Gulfstar?
accommodate export risers as Gunfint feld owners. The
While new, Gulfstar’s long as 14-in. in diameter, its Gunfint tieback is designed design is frmly rooted in fowlines consist of eight pull and engineered with modi- traditional concepts. As tubes that can accommodate fcations expected to occur the company had no spe- 15K risers up to 8.625-in., and after completion of the base cifc offshore location in its umbilical/injection lines Gulfstar project. With hook-up mind when it conceptual- consist of eight pull-tubes. and commissioning activities
Gulfstar’s foating ized the system, it had to Contained within the hull currently underway, Gulfstar spar was towed 135- make it as fexible as pos- is 10,440 bbl of dry oil, which is on schedule to start serving mi. southeast of New sible to adapt to the dif- will help with unexpected well Tubular Bells in 3Q 2014 and
Orleans before being ferent logistics of a given shut-ins. Should that happen, Gunfint in 2016.
moored in about 4000ft of water in site. That all changed after the dry oil can be pumped to the “Landing this Gunfint tie-
February 2014.
Williams signed on for the fow lines, taking the place of back before frst oil is received
Tubular Bells feld, thus live crude reserves. Gulfstar has from the anchor tenants
Gulfstar’s American origins undoubt- giving it parameters from 1160 bbl of methanol and other chemicals demonstrates the promise of the Gulfstar edly provided a boon of good publicity which it could build and like asphaltine and paraffn inhibitors on model for producers, both economically for Williams, as well as a boon to the operate. board as well to help with fow assurance. and technically,” said Rory Miller, senior economy – the project led to an esti-
Gulfstar is a system vice president of Williams’ Atlantic-Gulf
A speedy delivery mated 1000 new jobs in 20 states dur- with a classic spar hull operating area. “As a midstream com- ing the course of its development – but connected to a three-level One of the central tenets of Williams’ pany, Williams is focused on infrastruc- it was also a practical measure. Since topside, with each deck – vision for Gulfstar was to signifcantly ture solutions of this nature that connect both towns are on the Gulf of Mexico, a main deck, a production reduce the time from the discovery of the best supplies with highest-value shipping the components to Tubular deck, and a cellar. The reserves to the frst production. The goal markets. Gulfstar is one of approximately
Bells was a much quicker process to hull was fabricated in an is to fnish the project in 30 months, $4.5 billion in large-scale projects we execute than if they had been built overlapping sequence to which would be sometime this year; expect to bring into service in 2014 and overseas. speed construction of the initial production has long been slated 2015.” module. This design was for mid-2014. So far, things appear to be Gulfstar was also the frst spar built on Gulfstar could potentially be a model supposed to speed up the on schedule. After mooring the foating a graving dock, allowing for a simplifed for future developments of mid-sized time from the discovery of spar to the ocean foor in February, crews load out process. Its deck was lifted as felds, as companies look to cut down reserves to frst produc- in March lifted and installed Gulfstar’s one singular piece during the installation on the time and cost needed to construct tion to about 30 months. three-level topside platform. process, which limited the time needed offshore systems. Williams hopes to
The topside does not Williams was able to accomplish this to hook up offshore. The hull blocks were connect it other systems that it owns and feature a rig, only wells goal by serving as a one-stop shop for built vertically, thus allowing for better operates in the Gulf of Mexico, and it based on wet-tree technol- everything. Williams funded Gulfstar and access to the equipment as it’s being could become a primary facility for other ogy: the centerwell, 30-in. the export pipelines itself, essentially installed and reducing the problems that deepwater felds. And perhaps, down the diameter, is accessed via cutting out the middleman and creat- can come with horizontal construction. line, there will be other projects like it a valve tree attached to ing a consistent set of interfaces within According to Williams’ video on the developed in the Gulf’s waters. oedigital.com April 2014 | OE 51 000_0414_EPIC2_Gulfstar.indd 51 3/22/14 10:20 PM