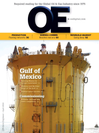
Page 65: of Offshore Engineer Magazine (Apr/May 2014)
Read this page in Pdf, Flash or Html5 edition of Apr/May 2014 Offshore Engineer Magazine
frequency converter unit, has been in Complexity
The power cells are cooled by the sur-
Subsea
The most complex component to design rounding oil, which circulates inside the development and testing since 2009. A was the VSD module, accounting for module by natural convection. The oil prototype is under construction, with about two-thirds of the research and is cooled through the enclosure, which the frst transformer complete and in development cost. is relatively thin due to the system being storage, following shallow water test- “This a complex unit,” Lystad says. at balanced pressure, by the surrounding ing in 2012. The subsea switchgear is “You have a lot of power modules seawater. in assembly, and the VSDs completing fnal testing and qualifcation to 3000m inside, with many parts, and even if Since 2009, Siemens started using water depth before assembly and test- we have high effciency, a lot of heat MIDEL 7131, a biodegradable liquid, ing in 2013-14. is generated and this must be removed which has good insulating properties and transported into the surrounding and is often used as transformer oil
Origins seawater.” where environmentally friendly solu-
The origin of the system was a project Siemens’ prototype VSD is built up tions are required. “The main issue with with Norway’s EMGS AS. Siemens was by total 18 power cells (six cells per the oil is when you fll the system, it has asked to provide a power converter for phase connected in series). All power to be done very slowly so you are sure a towed electromagnetic seabed logger, cells operate in oil and under pressure. oil penetrates every hole and pocket,” used for performing electromagnetic surveys offshore.
In the initial version, the power system was contained at atmospheric pressure in a cylindrical pressure vessel. The dif- ferential pressure created at depth caused leakage, so alternative means of contain- ing the power systems were considered.
In 2004, oil was used, creating the start of Siemens’ balanced pressure system. It was tested in water in 2005, and quali- fed to 3500m water depth, or 400 bar.
Due to the balanced-pressure system, it has a Plexiglas top. Development on this, and the grid, involved close co-opera- tion with the Norwegian University of
Science and Technology in Trondheim.
Some 16 towed units have since been on the vessels they are encased in, and delivered and a sixth-generation system therefore the system’s scale and weight. is under development.
The individual modules will be con- “The big difference with the power nected by Siemen’s 36kN subsea con- grid is that the system is on the seabed Jan Erik Lystad, next to a pressure vessel used for testing components at Siemens in nector, with power supplied via one HV for 20-30 years,” Lystad says. “We have
Trondheim. Photo by Elaine Maslin.
cable, containing the 36-145kV power, used oil for years in transformer produc- control, and signals cables, with moni- tion. But we did not know how it would toring, and frmware upgrades able to be when you put it on the seafoor—that be performed remotely, potentially from had to be investigated and qualifed by onshore, up to 200km away. our qualifcation project.”
Pressure-compensated equipment The alternative is to have atmo- subsea is well established in the industry. spheric pressure vessels, which require
But Siemens is aiming to put nearly the active cooling systems, in addition to entire system, including electrical equip- thicker walls, making systems signif- ment and power electronics, in this envi- cantly larger, with greater numbers of ronment. This means those components components.
that produce heat need to be naturally Siemens says it set out to use already cooled by convection to the surrounding proven technology, and qualify it for seawater. the subsea environment. The key was “This is a major technology challenge,” working out the cooling systems on an says Jan Erik Lystad, head of Siemens’ oil-flled balanced pressure system. “We
Subsea Technology Centre, Trondheim. have to control the equipment inside, “I think this will be the state of the art in including what heat it produces,” Lystad 10-20 years’ time.” says. “The distance between the equip-
The 155-tonne 6Mw system, which ment inside and the walls, and how you comprises a 25-tonne transformer, construct the housing is important, to 30-tonne switchgear, and 100-tonne create a good convection through the
The switchgear in assembly. Photo by Elaine Maslin.
variable speed drive (VSD), or seawater.” oedigital.com April 2014 | OE 67 000_OE0414_Susbea-2.indd 67 3/22/14 8:42 PM