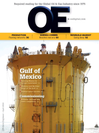
Page 70: of Offshore Engineer Magazine (Apr/May 2014)
Read this page in Pdf, Flash or Html5 edition of Apr/May 2014 Offshore Engineer Magazine
sheath damage and is flled with a sealing fuid, which seals off the damaged section
Subsea of the riser. The repair gel cures to form a solid while the elastic nature of the gel and design of the Armadillo permits the riser to fex as normal whilst continuing to prevent seawater ingress.
For more restricted areas, the company has developed
FlexGel, which is intended to be deployed around an annu- lus breach within an I-Tube or J-Tube, displacing the seawater. In doing so, the gel reduces further corrosion in the structural tensile armour wires of the fexible pipe, increasing its life.
There are a range of solu-
Flexlife is expert in providing life-of-feld subsea engineering and technology globally.
tions available to solve riser integrity issues, from low- approximately 200 riser annulus tests Since Neptune does not require access cost identifcation at the early stages to for most of the major operators globally, through annulus vent ports, this method detailed inspection of the condition of and the company has also established a is currently the only means of accurately the pipe through to the repair of outer strong share of the UKCS market in this determining the integrity of fexible pipe sheath damage and an engineering feld. annuli on risers with restricted or inac- assessment of the pipe’s life expectancy.
In one particular case study, the cessible vent ports. However, establishing a program at the company carried out an annulus testing
The inspection tool was able to catego- outset to appropriately design and regu- project for a client on a North Sea feld rize precisely where seawater was preva- larly inspect a pipe, which would avoid where seawater fooding was found lent within the riser’s annuli, enabling these issues, represents a signifcantly in some of the annuli of the risers. an inspection of the armor wires during lower cost and answers the risk question
Flexlife encountered that some of the operation to measure for corrosion. from the very beginning. older risers had a completely blocked
Fortunately in this project minimal venting system, preventing an assess- Stuart Mitchell corrosion issues were detected. The ment of their condition. serves as global information was reported back to the
The project involved the Health and business develop-
HSE, which allowed the pipes to con-
Safety Executive (HSE) because a riser ment director for tinue to operate. The risers were changed inspection was not possible, contrary to Flexlife, the life of out at the operator’s schedule, thereby industry practice. Because the condi- feld subsea engi- minimizing down time, the number of tion of the pipes was not known, there neering and technol- replacement risers and delays in produc- was also a risk having to shut down ogy frm, of which he tion, saving several million dollars.
production, a consequential loss of rev- While Neptune provides detailed is a founder. A degree-qualifed enue and a real concern that the instal- pipe inspection, ongoing oxygenated chartered engineer, Mitchell has worked lation may never resume production. corrosion can be mitigated through the in the subsea R&D, technology and
Flexlife deployed the ultrasonic scan- use of Flexlife’s modular Armadillo engineering space for 18 years and has ning tool, Neptune, a ROV-mounted system, which can be constructed specialized in unbonded fexible risers subsea inspection tool designed by in bespoke lengths and diameters to for the last 13 years.
Oceaneering that utilizes Flexlife’s pat- encapsulate and seal known outer The inspiration for Flexlife came when ented UT scanning technology in order sheath damage. Mitchell realized, through his own to determine the state of a fexible riser’s
The Armadillo will prevent the experiences that the available solutions annulus with 100% accuracy. ingress of further oxygenated seawater to some of the most common subsea
Data gained from Neptune scanning into the annulus, and where the pipe problems were not fully meeting the provides invaluable information relat- structure has been proved to be suitable requirements of the market. Seeing a ing to the condition of the fexible riser for continued operation through engi- gap in the marketplace for an innova- neering, allow that pipe to continuing tive consultancy offering its own annulus. The inspection tool also enables operating. patented solutions to these problems, operators to make informed decisions
Mitchell, with the help of his partners, regarding the remnant life of these The Armadillo is clamped around established Flexlife in 2007. production-critical assets. the fexible at the location of the outer
April 2014 | OE oedigital.com 72 000_OE0414_Subsea3-Flexlife.indd 72 3/22/14 9:05 PM