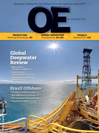
Page 165: of Offshore Engineer Magazine (May/Jun 2014)
Read this page in Pdf, Flash or Html5 edition of May/Jun 2014 Offshore Engineer Magazine
Oil and gas companies are using cloud-based solutions to remotely monitor production and machine health at disparate locations to
Source: Rockwell Automation maximize uptime and increase output.
Riddell, president of The Marrell Group, a management consulting ? rm for oil and gas businesses, based in The
Woodlands, Texas. So, conventional RFID had to be adapted for surface applications, such as equipment around the rig, and downhole assets, such as riser pipes running from the rig to the ocean ? oor. Since anything going downhole is subject to high pressures and temperatures, RFID has to survive drilling ? uids and other corrosive environments. Even with surface
RFID tags, the goal is to make them survivable for the life of the asset.
“A lot of these things look the same—a piece of pipe, a pump, or an engine. They all have original serial numbers stamped on them,” Riddell said. “But those become worn off and painted over. If you’re looking at 10 pumps, all manufactured by the same company, you can’t tell which one is which. And you have to know because each asset has its own maintenance schedule and date it went into service,” Riddell said.
And since this equipment moves around so much— going to shore for repairs or to be replaced—you need a mechanism to tag them permanently.
RFID isn’t just an ID number anymore. Downhole
RFID uses a combination of an RFID chip and a reading device. “If that reading device is installed downhole, even permanently in a well completion, you could pump RFID chips down the well with instruc- tions on them, and it tells the downhole equipment to do something—close a valve, open a sleeve, or take a measurement,” Riddell said.
a facility with limited capacity means personnel on RFID is useful in underreaming, where operators board is tightly constrained; bed space, lifeboat sup- activate and deactivate traditional underreamers port, helicopter scheduling, food and fuel – all have to (reamers operating below the casing of a borehole to be strictly managed and managed safely in a volatile enlarge it for the pipe) “by dropping a steel ball down to and corrosive environment. the tool via the drillstring,” said Tommy Laird, global technical and competency manager for performance
RUGGED RFID TRACKS MOBILE ASSETS drilling tools at Weatherford International in Houston.
Because offshore assets move around and live in Laird and co-authors, Luis A. Gonzalez (Marathon hostile environments, tracking those assets can be Oil) and Eddie Valverde (Weatherford International), a challenge. If you want to track an asset through its explain more about this drilling technique in a 2012 useful life, you have to be able to identify it. That’s paper, “Improving underreaming reliability with RFID where RFID comes in. technology.”
Operator rounds are becoming more automated RFID creates “an option to improve the performance with RFID’s use in ? eld inspections. Operators use of the underreamer by allowing multiple activations mobile handheld devices with RFID tags to properly or deactivations without restricting the drillstring ID. identify assets when they’re performing visual inspec- The operator may elect to underream only speci? c tions for process equipment, Winters said. “Field op- sections of the well, where swelling formations cause erators are key to enabling operator-driven reliability, stuck drillstrings, or perform full circulation in deac- where operations [personnel] take more ownership of tivated mode to clean out sections of the wellbore,” the basic care of the equipment,” he said. Laird said.
With handheld computers, ? eld operators can scan RFID is also seeing use with GPS. An RFID chip by the RFID tag, check the oil level as well as a leaky itself doesn’t transmit its location. But active RFID ? eld or visible vibration. “They use these handhelds actually transmits information. to record and collect data to demonstrate compliance The GPS communicates the coordinates of its physi- and ensure they’ve collected the right information on cal location. the right asset,” Winters said. “With active RFID, you could have a single reading
The problem with RFID is that it was originally device centrally located on a drilling rig and have adapted for non-hostile environments, said Mark it communicating with all the assets on the surface oedigital.com 167
May 2014 | OE REVIEW 0514OER_Asset_mgt.indd 167 4/19/14 11:31 AM