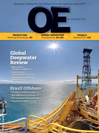
Page 170: of Offshore Engineer Magazine (May/Jun 2014)
Read this page in Pdf, Flash or Html5 edition of May/Jun 2014 Offshore Engineer Magazine
from an operations center in Aberdeen prepared by engineers with the Fraunhofer Institute
Scotland, 100mi. away. According to of Manufacturing Engineering and Automation, “The
Emerson: evaluation of the ? rst autonomous service robot that “Designed for unmanned operations, has ever been operated in offshore environments has the platform could serve as a model for proven the applicability of mobile robots to offshore future developments in marginal ? elds, platforms. Different types of inspection tasks (visual where such operations can help increase and acoustic inspection, gas measuring) have been profits as well as worker safety. The programmed and executed by the robot successfully
Solan field is expected to produce ap- without ever jeopardizing the safety of the platform proximately 40MMbo, with an estimated or the platform personnel.”
Simultaneously, a team led by Akbar Moghaddam, initial production rate of 24,000 b/d by the formerly at the University of Oslo and now with ABB, end of 2014.” has developed a climbing robot for use on offshore
The Babbage platform, in the southern platforms:
Prototype robot, Walloid. North Sea, was designed from the start to be unmanned. Brought online in 2011, “Walloid is a promising prototype for oil and gas it has an expected life of 20 years and exploits gas offshore environments. Although it’s still an ongo- reserves long ignored because they could not be eco- ing project and is being perfected through tests and nomically recovered by conventional means. academic reviews, but the development process of the project has made it a promising piece of work for
BEHIND THE SCENES further development and investment by the industry.
The support infrastructure that make drilling and Current design satis? es several critical requirements production possible are undergoing change, too, with of a climbing robot such as stability, ? exibility, homog- automation entering every phase of a platform’s life, enous force distribution, minimum power consump- from construction to decommissioning. tion that prevents motors overheating.”
First, the design and construction of platforms them- At the end of a platform’s life, another robot may selves are bene? ting from automation. As detailed in a help to dismantle it. According to a 2013 report of 2012 paper by industrial IT consultant Dr. Oskar Kwok a prototype’s performance in the laboratory, in the
Lum, the use of CAD/CAM drafting, analysis and design International Journal of Control and Automation, tools is automating the preparation of plans. “The 13 3/8in. casing was severed easily by the cut- “Record high oil prices in recent years have contrib- ting robot in a short time. The cutting process was uted much to the investment in oil rigs and production completed perfectly under the precision control and platforms. In line with the number of new oil rigs and monitoring system.” platforms being built, production technology in this
BRAVE NEW WORLD industry has seen relatively higher levels of invest- ment. Many shipyards new to oil rig building are As the reliance of offshore work on automation leveraging on technology to ensure success in the high steadily increases, the report of the Deepwater risk business of oil rig fabrication where penalties are Horizon Study Group sounds a sobering note: measured in terms of day rates to lease the drilling rig.” “Emergency situations caused by control system
Well construction is bene? ting from automation, failures or design weaknesses are often trusted to too. The Edison Welding Institute, for instance, has be handled and mitigated by human intervention. introduced automated laser inspection of riser pipe However, this requires both fast and accurate alarms welds. According to a technical paper prepared by its and warnings, as well as detailed operator knowledge engineering staff: of the system. This may in practice be unrealistic, “For riser fabrication, the traditional methods of deter- especially considering that the control system behav- mining weld quality have been human visual inspection ior and alarms after a control system failure may be using a borescope-type camera or inspection using a undocumented and inadequate for making the correct shadow probe. Both methods are subjective and rely on decisions. All human behavior is in? uenced by the operator decision. Inspection is necessary because a context in which it occurs, and operators in high-tech defective weld reduces the pipe’s fatigue life. For offshore systems are often at the mercy of the design of the
J-lay operation, common weld inspection techniques automation system software. Many recent accidents such as UT are currently used for immediate, post-weld blamed on operator error could more accurately be inspection on the platform. In an effort to be conserva- labeled as resulting from ? awed system and interface tive, traditional inspection techniques can sometimes design. Inadequacies in communication between provide false positives, incorrectly classifying an accept- humans and machines are becoming an increasingly able weld as one in need of immediate repair.” important factor in accidents.”
The laser inspection technique constructs a 3D Almost certainly, then, given the stakes, the last image of a weld, analyzes it for conformance with step of the Sandia technology roadmap will have to preset tolerance ranges, and forwards the image to the be embedded industry-wide into the offshore culture:
OE REVIEW operator when it senses an unacceptable discontinuity. Constant systems evaluation and revision.
Similarly, ? eld tests have established that mobile ro- bots may serve reliably on offshore platforms to do rou- Bob Felton is an engineer and freelance writer tine inspection and testing. According to a 2008 paper based in Wake Forest, NC.
oedigital.com 172
OE | May 2014REVIEW 170_OE0514_OER_Roboplatform.indd 172 4/19/14 1:15 PM