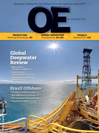
Page 84: of Offshore Engineer Magazine (May/Jun 2014)
Read this page in Pdf, Flash or Html5 edition of May/Jun 2014 Offshore Engineer Magazine
Sensing
Production a marinized solution
OptaSense is collaborating with Shell to develop a fully- marinized DAS system. OptaSense’s David Hill explains.
An OptaSense instrumented well with s the oil and gas industry enters to radically improve our understanding of a viborseis unit conducting OptaSense ever more challenging and pre- a broad range of issues, including reser-
DAS-VSP.
Photos from OptaSense.
A viously inaccessible plays, the voirs, ? elds, geology, and asset integrity.
? nancial risks can be greater. Therefore, Working on the principle “if you the need to understand better the issues can measure it you can manage it,” with Shell. The system, which will be being faced becomes more acute. OptaSense, a subsidiary of QinetiQ deployed in up to 10,000ft water depth,
Optimal reservoir monitoring has tradi- Group, has developed a DAS system able will allow highly accurate acoustic data tionally been a key issue, and providing to provide decision-ready real-time data acquisition for the ? rst time offshore and a clear and accurate picture of activity through the conversion of any standard will provide data for a wide range of sub- is regarded as a signi? cant enabler in optical ? ber into a distributed acoustic sea and deepwater applications, includ- achieving that. (or seismic) sensor. ing pipeline surveillance and leak detec-
A range of techniques have been Acoustic or seismic signals that strike tion, geo-positioning, in-well monitoring, used in the past, but, with advances in the ? ber cause minute strains. These are subsea assembly condition monitoring, technology, the deployment of distrib- measured using laser interrogation, turn- and permanent reservoir monitoring. uted ? ber-optic sensing has become an ing the ? ber into a distributed acoustic/ The device will include functional increasingly prevalent, more accurate, seismic sensor. An interrogator unit (IU) and technical parameters, con? gurable in and cost effective alternative. ? res a laser beam into the cable and mea- software, avoiding different hardware for
Distributed temperature sensing (DTS) sures backscatter returns from naturally settings or functions.
using ? ber-optic cable has been around occurring imperfections inherent in the The marinization process will require for several years, but the development optical ? ber. The minute strains cause the re-engineering of the interrogator of distributed acoustic sensing (DAS) subtle modulations of the backscatter, unit, to reduce its size to ? t into a highly is a relatively recent phenomenon and, that are then measured by the IU, thus robust pressure canister. The modi? ed through its versatility, it has the potential sensing the acoustic/seismic signal. opto-electronics will be tested, to ensure
It is ? ve years since DAS was ? rst It is ? ve years since DAS was ? rst they meet the rigorous and stringent tem- used downhole and it is now deliver- used downhole and it is now deliver- perature, vibration, shock, and electrical ing signi? cant bene? ts in a range of ing signi? cant bene? ts in a range of certi? cations required of subsea equip- completion, production, and evaluation completion, production, and evaluation ment, particularly during transportation projects, including hydraulic fracture projects, including hydraulic fracture and deployment. pro? ling, permanent wellbore ? ow pro? ling, permanent wellbore ? ow In the subsea in-well monitoring monitoring and seismic monitoring. application, the interrogator unit will be
OptaSense is now developing the positioned near to the wellhead, with a ? rst fully marinized and quali? ed processing unit, and processed data will
DAS system, in a joint program be relayed back to shore or appropriate installation, via a further ? ber-optic link An OptaSense interrogator unit.
in a control line.
May 2014 | OE May 2014 | OE oedigital.com 8686 000_OE0514PProdOps2_Optisense.indd 86 4/19/14 8:53 AM