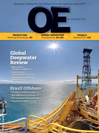
Page 86: of Offshore Engineer Magazine (May/Jun 2014)
Read this page in Pdf, Flash or Html5 edition of May/Jun 2014 Offshore Engineer Magazine
The enabling technology to get a ? ber the production lateral, without having measurements can be taken on a continu- into an offshore well has been developed sensors inside the cased well. Clamped ous basis or at regular intervals without and deployed. This enables ? ber to pass or strapped to the production casing and the need for costly well intervention and through the wet tree and through the cemented in place, a ? ber-optic cable deferred production, using the company’s packer, via a downhole wet-mate ? ber- can provide real-time DAS and DTS from drive-by acquisition service. It is also able
Production optic connector, into the producing zone. completions through abandonment, with- to provide full well bore seismic imaging.
Once permanently deployed on the pro- out well intervention. Earlier this year, OptaSense was duction tubing, the ? ber can be used with The uses of DTS, although compli- contracted by Petroleum Development a DAS system to continuously pro? le the mentary, are limited. While DTS has Oman (PDO) to provide the industry’s ? ow along the well, measuring the in? ow been used for over a decade, borehole ? rst multi-well 4D DAS vertical seismic contribution at each producing stage. temperature is only part of the story pro? ling system, to monitor and map the
In-well equipment, such as electrical when it comes to monitoring a hydraulic performance of up to 12 steam-injected submersible pumps, in? ow control valves, fracturing operation. With a DAS system, oil wells in a brown? eld development at and gas lift valves can be constantly moni- it is now possible to listen to the well at South Oman salt basin.
Seismic signals have been recorded from tored to optimize performance and access each perforation location and hear how ? ber-optic cables attached to each well’s their condition for predicative mainte- the ? uid and proppants rush through production tubing, permanently installed nance purposes. Also the downhole ? ber the ori? ces, and how the rock fractures and linked to a surface data-gathering can be used to acquire the shot records for just outside the well and beyond into the center. The ? nal processed data set will be a vertical seismic pro? le (VSP). Because formation.
Combining DAS data with real-time integrated into PDO’s reservoir models and it is permanently in-situ, repeat VSPs can pump data from the pumping trucks, it is assist in the determination of ? uid substi- be performed easily enabling time-lapse possible to estimate how much ? uid and tution through production and contribute imaging of the reservoir around the well. proppant is being pumped into each perfo- towards the positioning of in? ll wells.
In EOR applications 4D VSP using DAS ration cluster. With the full-well continuous can be a powerful tool in understanding Weighed against using geophones in monitoring DAS enables, all activities dur- the effect of injection and other forms of this type of application, the DAS technol- ing the hydraulic fracturing operation can stimulation on the reservoir. ogy provides bene? ts, including lower- be monitored for effectiveness including:
OptaSense has been able to use its cost on-demand acquisition through • parent ? rm’s facilities for quali? cation wireline tool tracking; permanent cable installation; deployment • testing. It is anticipated that the marin- bridge plug setting; perforating; in wells inaccessible to geophones, with • ized unit will be ready for demonstration ball drop, ball seating, sleeve sliding no well intervention required; synergies by the end of 2014. and isolation from previous stage; and with existing systems and retro? tting casing leaks and restrictions that can capabilities; coverage over the entire
Further potential uses of the DAS tech- • nology subsea are currently being explored halt or hinder operations, and accurately length of a well and simultaneous data report their depth. acquisition of multiple contiguous wells. but appear wide-ranging, such as monitor-
The development of distributed acous-
The system can also be used to visual- ing the condition of subsea equipment, by tic sensing through deploying ? ber-optic wrapping the sensors around the pressure ize ? ow dynamics, providing an alterna- cable represents a technological develop- tive to conventional permanent produc- vessel they are contained in.
Onshore, ? ber-optic DAS technology tion logging tool (PLT) readings, with the ment in the monitoring arena, allowing is being used in hydraulic fracturing DAS ? ber installed on casing or tubing. operators to see what is happening across operations to measure the full length of Through a permanently installed ? ber, the wellbore in real-time. The system has multiple uses and, as it prepares for its deployment offshore, a new range of opportunities.
David Hill is a
QinetiQ Senior Fellow and the Chief
Technology Of? cer at
OptaSense, a
UK-based QinetiQ company, which he jointly founded. He has over 29 years research and develop- ment experience in acoustic sensing, with over half that time spent developing ? bre-optic based sensors for the military, as well as oil and gas and other civil
Time verse Depth waterfall showing DAS recording of in-? ow at the production zone applications. He has a BSc(Hons) in of a horizontal well.
Imaging Sciences from the University of
Westminster, London, and a PhD in
Physics, specializing in ? ber-optic sensing, from the University of Kent, UK.
Fiber optic cable.
May 2014 | OE oedigital.com 88 000_OE0514PProdOps2_Optisense.indd 88 4/19/14 8:54 AM