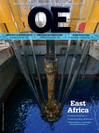
Page 38: of Offshore Engineer Magazine (Jul/Aug 2014)
Read this page in Pdf, Flash or Html5 edition of Jul/Aug 2014 Offshore Engineer Magazine
Offshore drilling optimization:
Drilling
Utilizing the future of technology
By Alex Barrie, NOV n today’s oil and gas markets, there are many drilling situations in
Figure 1: NOV BlackBox downhole dynamics tool. Photo from NOV.
I which an operator faces adversity.
A growing dif? culty to successfully and There are many factors which lead to of time to transmit data back to surface, economically drill and produce wells has this drilling conservatism and inher- consequentially leading to a lack of created a global demand for proper well ent need for optimization, especially in knowledge of true downhole behavior at optimization. Successful economical pro- today’s offshore wells. As the dif? culty any given moment. There is a continual duction of these wells requires a delicate to reach a production zone increases, so search for the perfectly balanced tool, balance between cost, performance, and does the risk. Many times the wells that one which produces high-performance risk. The oil and gas industry has a vast are deemed more risky to produce also data with low operator risk. How is this portfolio of available tools and technolo- inherit a more conservative performance tool de? ned and who produces it?
gies worldwide, with most aiming to plan by operators. For years, the oil To answer this search for the best drill- provide new and improved informa- and gas industry has been adapting and ing tool for well optimization, several tion, save operators’ time, and improve upgrading tools, but the responsibility of aspects must be considered that highlight the well’s pro? tability through various the well inevitably requires human inter- the future of the oil and gas industry, means of drilling optimization. The action and decision making. Offshore especially in offshore well production. offshore markets also have additional drilling operators have invested millions Today’s drilling operators consider four inherent risks due to regulations and of dollars into computerized technol- main variables in drilling performance accident prevention. Utilizing existing ogy and backup equipment to obtain tools: speed, consistency, precision, and future technology to optimize this the most precise measurements possible and reliability, all at the lowest cost to balance and leverage risk is the key to the from surface equipment and prepare for increase production margins. Within next generation of drilling optimization; any possible adverse downhole situa- these categories is the key to drilling however, determining the correct method tions. Downhole tool con? gurations and optimization: A driller must have both of optimization and required tools has bottomhole assembly (BHA) design also the quality of data and quantity of data to historically depended on the application play a crucial role in this endeavor, yet make an informed decision. This comes due to limited downhole information. deeper wells often take extended periods with a caveat, as either of these variables alone is useless if it is not deliv- ered quickly enough to surface for the driller to interpret. This adds increasing merit to the adoption of today’s technology into the industry.
The oil and gas industry has traditionally been slow to adapt to changes in technology, which will only be more scrutinized as the industry’s generation gap settles. There is a massive amount of experience leaving the industry, and the younger generation will rely more than ever on technology to capture, save, and utilize this informa- tion to bridge the knowledge gap in drilling. The most important aspect of this “crew change” will be the change in mindset, allowing the industry to progress its drilling optimi-
Figure 2: Automated drilling system components. Image from NOV.
zation practices using digital
July 2014 | OE oedigital.com 40 040_OE0714_D&C3_NOV.indd 40 6/20/14 3:15 PM