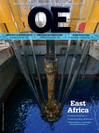
Page 40: of Offshore Engineer Magazine (Jul/Aug 2014)
Read this page in Pdf, Flash or Html5 edition of Jul/Aug 2014 Offshore Engineer Magazine
technology and computer-controlled situations as they occur from various data, formation expectations, and direc- equipment as an aid to experience. sensors integrated into drilling equipment tional planning), which is the frst step
Because so many factors contribute to both at surface and downhole. What can toward using downhole technology to drilling optimization, a single tool would these sensors show, and how will they increase performance and safety. Next, not alleviate the needs of the industry. beneft today’s operators? The answer is there is the ability to create a drilling
Drilling
Instead, a shift in the mindset of drill- a tiered approach, beginning with well roadmap, which is fully optimized for ing practices toward using technology to planning and continuing through produc- a particular region or series of wells. facilitate decision making is a solution to tion, with each tier using these sensors in When establishing a pad to drill several the industry’s drilling optimization needs. a related manner. wells, the operator typically drills the
The main catalyst driving this is technol- There are various tools and drilling frst well using only survey information. ogy integration. optimization solutions available in the A drilling optimization tool (or series of
As with other industries, operators market to complement this new tiered tools in various locations in the BHA or will soon be faced with the “big data” drilling mentality. First and foremost, string) such as National Oilwell Varco’s situation—having the ability to visualize there is proper well planning (survey BlackBox memory tools (Figure 1) can record drilling dynamics data at a high frequency, as it occurs. This not only pro- vides the driller with valuable post-well drilling information, but also allows a drilling roadmap for the remainder of the pad. This roadmap can offer previously unknown details about the formation, reactive vibration and torque, and down- hole weight transfer, providing the driller with faster, more reliable performance going forward.
High-speed data telemetry with wired drillpipe supporting real-time downhole tools is at the top level of drilling opti- mization. When compared to traditional mud pulse measurement-while-drilling tools, real-time drilling data feedback can provide information to the surface at the fastest rate and highest quality possible, allowing the driller to visualize drilling reactions to the preplanned drilling road- map. This also allows for understanding of real-time energy loss based on the down- hole data versus surface data comparison.
Several wells have been drilled using
National Oilwell Varco’s BlackStream downhole drilling dynamics tools in col- laboration with IntelliServ wired drillpipe.
While similar to the BlackBox memory tools in data acquired, the BlackStream downhole tools connect to wired drillpipe for real-time telemetry. Over the course of several wells, the BlackStream tools provided an increase in both consistency and performance. An illustration of the automated drilling system and compo- nents can be seen in Figure 2, showing the downhole tool and its connection to the surface data acquisition system.
The automated drilling system has several advantages with respect to drill- ing optimization. By itself, the system allowed the driller to clearly view downhole behaviors as they occurred
Industrial Bolting Systems Advanced Tensioning Systems Hydraulic Torque Wrenches Pneumatic Multipliers while drilling. These behaviors allowed
Electric Multipliers Hands-Free Safety Time Saving Simplicity Industry-Leading Accuracy Patented Innovations the driller to measure torque transfer and multiple types of vibration that were contributing to energy loss along
July 2014 | OE oedigital.com 42 040_OE0714_D&C3_NOV.indd 42 6/20/14 3:18 PM