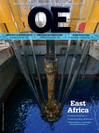
Page 64: of Offshore Engineer Magazine (Jul/Aug 2014)
Read this page in Pdf, Flash or Html5 edition of Jul/Aug 2014 Offshore Engineer Magazine
boom of the last decade was not perfor- mance, but price. Until 2012, an SPB containment system for an LNG carrier cost about 15% more than a comparable membrane system. Today, according to
Vessels the manufacturer, the SPB premium is less than 10% more than a membrane system. As orders increase, there is an expectation that production ef? ciencies will further lower costs. This could well be aided eventually by ef? cient licensees building tanks in other countries.
Most enquiries for SPB systems to date have come from energy companies con- sidering ? oating production, storage and terminal facilities for offshore develop- ments, but recently, with Japan looking to increase LNG imports over the coming decade, interest in the system among domestic shipowners has begun to rise.
As SPB tanks are, by nature, custom- built for each ship, they can be tailored to ? t any hullform. This raises the possibil- ity of converting existing ships for LNG service, presenting a potential boon to emerging markets needing shuttle tankers and shipowners looking to change the direction of a half-built vessel. While all this may not mean the coming of a future world ? eet containing combination carri- ers with lique? ed gas capacity, or parcel tankers hauling LNG as just another
JMU says the shape ? exibility of the IHI-SPB makes it an ideal alternative to the
Type C tank, shown here in concept renderings for TOTE’s gas-fueled containerships hazardous cargo, it does seem to signal and Waller Marine’s articulated tug barges. Images courtesy of TOTE and Waller Marine interesting times ahead. evolve and advance into new markets EDITOR’S NOTE: A version of this article
New future, new ideas
The performance of the two existing and services. appeared in the Fall/Winter 2013 issue
SPB-equipped LNG carriers indicates this The main factor that has kept SPB of Surveyor, a quarterly magazine from technology could help the LNG sector technology out of the LNG building ABS.
of containing the cargo for a period of 15 days in the event of a
Differentiating among tank types ruptured or leaking tank.
The IGC Code de? nes membrane tanks as well as three type IMO Type B independent tanks are de? ned as “designed using categories for independent LNG cargo tanks. model tests, re? ned analytical tools and analysis methods to
Membrane tanks are non-self-supporting tanks which consist determine stress levels, fatigue life and crack propagation char- of a thin layer (membrane) supported through insulation by the acteristics.” One of the key characteristics for Type B designation adjacent hull structure. The membrane is designed in such a way is compliance with the ”leak before failure” concept, under which that thermal and other expansion or contraction is compensated crack propagation analysis by fracture mechanics techniques for without undue stressing of the membrane. This containment must demonstrate that if a crack in the system should develop, system requires a complete secondary barrier capable of con- its growth will not be rapid enough to allow excessive leakage into taining the cargo for a 15-day period, and typically the membrane the cargo hold. A partial secondary barrier, which can consist of tanks do not exceed a 0.25 bar design vapor pressure; however a spray shield and drip pans, is required for independent Type B if the hull scantlings are increased accordingly the design vapor tanks with minimum design temperatures below -10°C. Prior to pressure may be increased to 0.7 bar. Today, Gaztransport & the IHI-SPB, all Type B tanks were spherical vessels of the Moss-
Technigaz (GTT’s) systems, which are approved by all major clas- Rosenberg design.
si? cation societies, have a capacity range for existing vessels of Type C tanks are spherical or cylindrical pressure vessels, like 20.000-266.000cu. m. The tanks are also being considered for those typically seen topsides on LPG carriers. Because these smaller-sized LNG carriers and LNG barges, as well as fuel tanks tanks can be made to ? t into any available space in the ship, the on gas-powered vessels. Type C tank is ideal for the fuel tanks in gas-powered vessels. ABS Type A tanks are designed primarily using recognized stan- granted AIP for this application in 2011 when JMU developed a dards of classical ship structural analysis and constructed of a concept design for a gas-fueled containership. This is the type plane surface. The c ode limits this type of tank to a vapor pres- indicated for the fuel tanks being fabricated as part of the design sure of less than 0.7 bar, and where minimum design temperature for TOTE’s gas-fueled containerships and Waller Marine’s articu- • is below -10°C, requires a complete secondary barrier capable lated tug-barges for local LNG distribution and supply.
July 2014 | OE July 2014 | OE oedigital.comoedigital.com 6666 064_OE0714_Vessels1_ABS.indd 66 6/20/14 5:15 PM