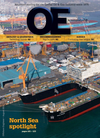
Page 134: of Offshore Engineer Magazine (Aug/Sep 2014)
Read this page in Pdf, Flash or Html5 edition of Aug/Sep 2014 Offshore Engineer Magazine
Integrating automation offshore
Peter Welander examines how the challenges of networking disparate elements are intense, but workable.
he offshore oil industry is evolving rapidly, as oil all operation. To make it work, the integrator may have
T and natural gas now begins to ? ow from deposits to unravel the system’s programming and determine considered impossible to tap just a few years ago. Pro- how to make it communicate with the larger system. duction companies around the world are working to Some boxes are blacker than others, so the task might exploit ? elds in remote locations, in very deep water, be simple or it might be a headache, but it probably and below huge amounts of rock. involves writing specialized programming code just to
At the same time, more production equipment is mov- talk to that device. ing off ? oating platforms to the sea ? oor. In years past, a
TECHNOLOGY DIFFERENCES well that produced a mixture of oil, gas, and water would have to send the mixture to the platform for separa- One challenge to offshore integration is that relatively tion. Now that process can occur at the wellhead, with few companies produce equipment for offshore instal- separate streams of oil and gas pumped to the surface. lations. The companies that dominate the market in
The costs of maintaining offshore platforms and the subsea equipment can be counted on one hand.
people that operate them are sizable, and remain a driver Lee Swindler, oil and gas program manager for for operators to ? nd ways to move equipment and people Maverick Technologies, has worked on these projects off platforms - and even eliminate the need for them ? rsthand. “I think it is because offshore rigs have tended entirely. “It’s a whole new business case for developing to be built as a single isolated entity,” he says. “Because oil and gas,” Ann Christin Gjerdseth, director, controls of that, they tend to tolerate equipment that doesn’t and data management for FMC Technologies, says. “The play well with others. They go to a single engineering business case for placing production equipment subsea company that uses a few select suppliers to design and is a very favorable one with regards to cost and the en- build the entire rig, whereas onshore facilities tend to vironmental footprint. But moving more to the seabed be put together more piecemeal.
brings a holistic challenge around automation, and that “That is certainly a big difference with downstream, infrastructure needs to be designed to use more function- re? nery-type plants where there are established commu- ality. That’s driving new thinking around automation.” nication and interface protocols that are commonly used and it allows you to mix-and-match suppliers and still
INTEGRATION ON A GRAND SCALE end up with an integrated system. (Offshore) you’re left
Getting oil from a wellhead on the sea ? oor to an on- trying to use a single supplier solution in a lot of cases shore terminal, and eventually, a re? nery, requires dif- in order to get it to integrate, and even then it’s probably ferent processes that have to work together ef? ciently only doing part of what you need, or trying to ? gure out and safely. Simultaneously, the data also has to go to how to make things work together on your own, which the enterprise. can be time consuming and dif? cult.”
When a main automation contractor or system inte- A platform isn’t a single black box, but a whole grator ties together such a large-scale project, invariably series of small, isolated systems that have their own there will be some “black boxes” thrown into the mix. A controllers, Paul Bonner, oil and gas vertical leader black box could be a major piece of equipment or skid- for Honeywell Process Solutions, explains. “You’ve got ded subsystem (skids) designed to perform a speci? c compressors on platforms and you’ve got a third-party function. It remains self-contained, with its own control- black box compressor control system,” Bonner said. ler and small-scale automation system. “There might be an anti-surge control system, or a
Such skids can perform their functions ? awlessly; on separate safety interlock system, and so on. They’re all the other hand, designers might not be aware of how it different systems that you think of as being outside the should ? t into the larger automation scheme for the over- distributed control system (DCS) but have to interface oedigital.com 136
OE | August 2014REVIEW 133_OE0814_OE Review.indd 136 7/23/14 12:19 AM