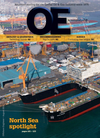
Page 56: of Offshore Engineer Magazine (Aug/Sep 2014)
Read this page in Pdf, Flash or Html5 edition of Aug/Sep 2014 Offshore Engineer Magazine
ensure wells are designed and produce as expected.
In 2013, a North Sea operator used an integrated, collaborative approach to complete its frst subsea well project in
Planning
Drilling
Norway. This was a two-year undertak- ing that resulted in two satellite oil wells being successfully brought online. For service company Weatherford, the project for success was the frst fully integrated subsea
Weatherford’s Yvonne McAnally the complexities of positioning the well- completion involving both the upper and head and infrastructure on the sea foor lower sections of a subsea well. and Ben Lake show how have taken technology development to a The wells, at total vertical depth of collaboration and integrated new level of sophistication. 3600m (11,811ft), are located in the
In venturing into this important fron- North Sea’s Jette feld, estimated to hold methodology delivered an tier, however, the industry has learned 14MMbo. The region is highly regulated operator’s frst subsea well that successful completions require more by Norway’s Petroleum Safety Authority project in Norway.
than the application of advanced tools (PSA), which oversees technical and and technologies. Operators are look- operational safety in hydrocarbon ing for methods that bring integration production, ensuring that companies he risky business of oil and gas and collaboration to the subsea arena, implement the appropriate safety bar- development is no more evident from extensive planning and testing, to riers to ensure long-term well integrity.
T than in the subsea sector, where the installation of correct equipment to Weatherford was selected to design, build and install the subsea completion into 9 5/8-in. main-bore casing strings for the two subsea wells in 127m (417ft) of water. The wells were eventually tied back to the ExxonMobil-operated Jotun B production platform.
The completion system needed to include a safety valve, packers, liner hangers, swellable packers and screens, as well as the capability for the required cable and gas-lift systems and well control. The cornerstone of the operation was Weatheford’s Optimum cased-hole upper-completion system, which com- bines various modular tools that, when used together, create a customized solu- tion based on the needs of a specifc well.
Weatherford worked closely with the operator in conducting extensive analysis of the reservoir data to ensure selection of the proper equipment. Extensive studies of the expected production profles and planned operating life of the wells were performed, along with casing confgura- tions, connections and subsurface tree design, which has an impact on how the completion is carried out. For example, trees must be designed to enable opera- tions, such as chemical injection, that may be required later in the production life of the well.
Well on paper
The planning phase included a compre- hensive well design on paper, where both companies examined the running proce- dures for every aspect of the completion,
Optimum completions.
Photos from Weatherford.
including all the equipment that would be needed for the lifespan of the well.
August 2014 | OE oedigital.com 58 058_0814_D&C_Weatherford.indd 58 7/22/14 3:25 PM