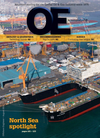
Page 58: of Offshore Engineer Magazine (Aug/Sep 2014)
Read this page in Pdf, Flash or Html5 edition of Aug/Sep 2014 Offshore Engineer Magazine
The process was repeated several times were implemented. The OptiMax tubing- completion system was successfully prior to equipment installation. Ongoing retrievable, surface-controlled subsur- installed in both wellbores, with the project management also included a face safety valve (SSV) was installed to entire operation ? nished two days ahead quality control plan that documented the provide positive shutoff protection in the of schedule, reducing rig time and associ- quality-assurance requirements for the event of a catastrophic well control inci- ated costs. In the lower completion, the
Drilling safe manufacture, inspection and testing dent. SSVs are required in the Norwegian standalone screens and ICD protected of all cased-hole completion components North Sea for well control and to prevent the sand from hot-spotting. By providing for the wells. Most of the equipment was the release of any reservoir ? uids. Safety an effective seal between the outside of built in Houston or Aberdeen to meet the was further enhanced by a 9 5/8-by-5 the production tubing and the inside of delivery deadline. ½-in. hydrostatic set removable produc- the casing in the upper completion, the
Since many wells in the region at some tion packer that provided a seal between hydrostatic set removable production point require arti? cial gas lift to enhance the outside of the production tubing and packer eliminated the need for addi- recovery, the design incorporated gas lift the inside of the casing. tional wireline work, resulting in further mandrels and other equipment to elimi- cost savings. Pre-installation of gas-lift
Avoiding workovers nate the need for future costly workover mandrels and the chemical-injection operations. Risk and contingency plan- Because most North Sea wells are com- system will eliminate the need for future ning also were built into the completion pleted with chemical lines in the event workovers to maintain production.
design. chemical injection is required during the The two wells were brought online
The lower completions included more lifespan of the well, a chemical injec- 2Q 2013, and are currently producing than 100 standalone screens with in? ow tion mandrel with shear-out valve was 14,000 b/d. The success of the collabora- control devices (ICD) that were installed installed to deliver production chemi- tive strategy encouraged the operator to to regulate ? ow into the screens and cals, such as scale and paraf? n inhibitors. implement the approach for additional establish consistent production. The ICDs By installing the lines at the outset of the wells in the region. The Optimum also prevent formation sand from creating project, the operator can avoid a subse- completion system has since been localized erosion, a phenomenon known quent costly well intervention operation. updated to include a radio-frequency as hot spots. Swellable packers were The same rationale applied to the identi? cation (RFID) module that uses installed in the open hole zone to isolate pre-installation of two 5 ½-in. gas-lift radio transmitters and receivers to con- the formation’s different production mandrels, both unloading and ori? ce trol packer setting and opening/closing of zones and prevent cross-? ow between the styles, for arti? cial-lift, an operation sleeves, which further reduces costs and zones in the event of a pressure differen- that simulations conducted during the enhances safety.
tial. Liner packer hangers were installed planning phase had predicted could be As operators continue to exploit to take the weight of the tubing string and needed within 12-18 months after the complex and risky subsea well projects, serve as barriers between the reservoir wells were brought online to maintain collaborative, integrated methods that and the casing. production rates. include extensive planning, strong proj-
For the upper com- After the upper completion was run, ect management and innovative applica- pletion, all elements a 10 ¾ in.-by-5 ½-in. tubing hanger was tion of advanced technologies are critical of the Optimum run and landed in the hole. Pressure to maximizing production while enhanc- completion tests were conducted on the tubing ing safety. platform hanger. The production packer was set and ? nal pressure tests were carried out Yvonne McAnally on the production tubing, packer and serves as global the chemical injection control line. The product line director, installation procedure was com- upper completion for pleted with an in? ow test of the Weatherford. Over
SSV and other pressure tests the last 16 years, she on the tubing hanger and has held various valves set in various roles in engineering, positions. marketing and business development.
The cus- She has a BS in mechanical engineering tomized from University of Houston.
Ben Lake serves as the global product line director, safety systems, for
Weatherford. Over the last 12 years, he has held various roles in engineering and marketing. He has a BS in mechani- cal engineering and a MBA from
OptiMax safety valve.
Oklahoma State University.
August 2014 | OE August 2014 | OE oedigital.com 6060 058_0814_D&C_Weatherford.indd 60 7/22/14 3:26 PM