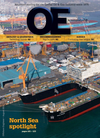
Page 64: of Offshore Engineer Magazine (Aug/Sep 2014)
Read this page in Pdf, Flash or Html5 edition of Aug/Sep 2014 Offshore Engineer Magazine
a contingency preprogrammed timer prevents inadvertent activation of the well fuid into an atmospheric chamber sequence may be used to set the packer. packer. After activation, the setting force to initiate the setting sequence. Using is generated by well hydrostatic pres- hydrostatic setting pistons is a feld-
Deeper well depths sure acting upon atmospheric pistons proven alternative for greater well depth
The deep-set system employs a magnetic mounted outside the mandrel. applications, where suffcient bottom-
Drilling trigger to set the packer, comprising a The packer is similar in design to the hole pressure is available to generate the surface-deployed special “follow” cas- one used in shallow-well applications, required setting forces. ing wiper plug (CWP) and a downhole with the exception of hydrostatic set- As with the shallow-well system, dif- annular casing packer. The setting ting pistons, replacing the compressed ferent triggering methods exist for the sequence is activated by a magnetic feld nitrogen module. After the onboard deeper well model: 1. generated by the CWP as it traverses a electronics receives confrmation of the Using the follow CWP that acti- multitude of Hall Effect sensors in the correct magnetic signature, a trigger valve vates the setting sequence after a packer’s electronic module. The signature opens to allow hydrostatically charged preprogrammed amount of time has elapsed to allow for completion of cementing operations.
Using a drop bar that employs the 2. same magnetic signal carrier as employed on the follow CWP.
A contingency preprogrammed timer 3. sequence allowing the packer to set if the follow CWP or drop bar is not detected.
The electronics module is powered by a battery pack with the same time limita- tions as the shallow-set tool battery. The deep well module can operate in two temperature ranges, 100-300°F (38-149°C) and 250-392°F (121-200°C). In higher temperature uses, a low-temperature bat- tery initially powers the electronics at the surface, which becomes nonfunctional once its temperature threshold is reached downhole, before which a high-tempera- ture lithium battery activates.
The packer seal used in both systems has the same proven, gas-tight, metal- backed, zero-extrusion gap design. The setting force drives the seal up a cone ramp, causing it to expand and conform to the casing internal diameter. The ele- ment’s external tooth profle eliminates any extrusion gap, trapping the setting force between the teeth and preventing cold fow of the elastomeric cover.
Field results
The annular casing packer can be deployed as a secondary pressure barrier for conventional and unconventional oil and gas wells, offshore and on. Its frst feld application was unique in terms of the size required: an 18-5/8in. long string packer that is set in 24in. casing. To date, three systems have been successfully installed in offshore Sakhalin Island,
Russia, wells, the frst at 150m (492ft) and the second at 370m (1200 ft). The operator performed a 10 bar (150 psi) backside pressure test on the frst well, and a 15 bar (218 psi) test on the second well, for 30 minutes, to confrm the seal was successfully set. The operator
August 2014 | OE oedigital.com 66 060_OE0814_D&D3_BakerHughes.indd 66 7/22/14 6:30 PM