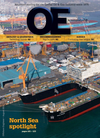
Page 95: of Offshore Engineer Magazine (Aug/Sep 2014)
Read this page in Pdf, Flash or Html5 edition of Aug/Sep 2014 Offshore Engineer Magazine
from FEA output to analyze the percentage and sensitivity. In time domain, accelerations with and without g-contamination are compared and shown in Figure 12. A maximum g-contam- ination of 14% of the acceleration standard deviation is found along the riser length. The g-contamination is found negligible.
Note however that for applications where higher dynamic riser angles are expected, the g-contamination can be removed through the use of angular rate measurements.
Conclusions
To take full advantage of the accumulated monitoring data, a new fatigue monitoring methodology was developed using ana- lytical acceleration to curvature transfer function to account for the fatigue damage due to both wave and VIV effects.
This new methodology has been validated very well with a fnite element analysis (FEA) method, by comparing curvature distribution. The advantage of using FEA results to validate the methodology is that there is no noise, g-contamination, and added mass and tension uncertainty in the accelerations and curvature time traces.
Comparing with feld measured data, the results show that the calculated fatigue is sensitive to added mass and drag diam- eter, but not g-contamination. With a 54in-diameter drag and an added mass of 1.8, the proposed method matches well with the measured feld data. A standardized approach for selecting the added mass coeffcient and hydrodynamic diameter is the subject of ongoing work.
For future work, both acceleration and strain measurements from a riser system with continuous buoyancy or slick joints are preferred to better understand the effect of the total added mass,
Visit us at which is dependent on the added mass coeffcient, Ca and the
ONS drag diameter. In addition, a more detailed and complicated
CFD simulation may be conducted to investigate the actual drag 25-28 August 2014
Stavanger, Norway affect and added mass effect. Extra strain sensors on different locations and a non-staggered riser confguration would also
Stand No. B 266/2 assist in further validation of this methodology.
Acknowledgments
The authors thank the management of BP for permission to
Elevators publish this paper. In addition, the authors wish to express thanks to 2H Offshore engineers who did the data analyses for tough environments documented in this paper. • Shaft-less — low investment costs
Michael Long Ge is subsea riser engineer. • Machine room-less
He has worked on a wide range of projects • Unique safety features for BP in the Gulf of Mexico, including engineering, design, inspection, mainte- • Capacities between 300 kg to 7,000 kg nance, monitoring, and integrity manage- • Forklift loading — class A, B, C1, C2, (C3) ment. He holds a MS in mechanical • Remote monitoring keeps down-time to a minimum engineering from University of Florida and • Fully compliant with EU and US regulations a BS in engineering mechanics from
Shanghai Jiao Tong University. • 30,000 rack & pinion solutions installed since 1948 > • Explosion protected for EU and US regulations
Himanshu Maheshwari is a senior engineering specialist at 2H Offshore in
Houston. He has extensive experience in delivering riser integrity management and monitoring programs including project management, system engineering, instru- www.alimakhek.com mentation, installation and data manage- ment. Maheshwari has a MS in mechanical engineering from Texas A&M University.
oedigital.com August 2014 | OE 97 000-OE0814_Subsea2_2H.indd 97 7/22/14 3:39 PM