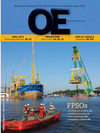
Page 78: of Offshore Engineer Magazine (Sep/Oct 2014)
Read this page in Pdf, Flash or Html5 edition of Sep/Oct 2014 Offshore Engineer Magazine
voltage and environmental testing, shock and vibration testing, high pressure testing, and gas testing is carried out and can take up to two years to qualify a
Subsea connector.
An environmental chamber is used to put materials through temperature gra- dients, as well as humidity. Temperature tests can range between -40°C and +90°C.
Pressure testing can be carried out up to 30,000psi at Ulverston, including circu-
Typical phase confguration. lated sand and silt and circulated in the pressure chambers, for connection tests.
For critical component testing, HV trials at 104Kv are run for four hours, partial discharge-free up to 90Kv, with no breakdown at 200Kv, and components are X-rayed for faults.
For qualifcation, about 150 connection cycles are tested. On Siemens Subsea’s
Tronic DigiTRON, 1000 cycles were performed, without the product failing. A typical connector is likely to see no more than 50 connection cycles, Marklove says.
In comparison, for a standard factory acceptance test, a 10,000Kv rated har- ness—an electrical jumper/fying lead— would be put through a 15,000Kv test.
Measurements test for current leakage, to make sure there is minimal dis- charge, to assess the insulation material performance.
A pressure test vessel at the Ulverston facility.
The boundaries at which these compo- connector for the SPG and it will be the and the connector qualifcation program nents need to perform will continue to be highest voltage connector worked on. The is expected to run for 1.5 years. pushed out, and Marklove says more new highest power rated wet mate connec- Qualifcation is being done accord- technology will need to be developed. tor commercially available, and being ing to (Statoil Spec) TR2313—Subsea “For longer step-out distances you used, at the moment, is a 10Kv connec- Electrical High Voltage Connector need to compensate for the effects of tor, at 400amp, says Phil Ashley, head of Assemblies. It will be tested at 200Kv transmitting over a long cable. There are
Siemens Subsea Connectors. “We do have during qualifcation. various options being considered,” he a 60kV dry mate connector developed, but Siemens Subsea’s Tronic connec- says. “DC is an alternative, but it does it has never been used in anger.” tors are designed to be modular, which introduce new issues around power
The core mechanical design, invented means parts are standardized and electronics, which are not powerful by the founder of Tronic, bought by can be ordered to create a component enough, yet. DC also represents differ-
Siemens in 2012, is a cone-shaped con- which meets its application needs. This ent challenges to AC, with how it effects nection spring, with dual barriers, which includes a common module interface materials. We are working on DC testing enables subsea wet-mate connections in a (CMI), and common module glands, with a product at high voltage, getting us controlled environment. the addition of wet mate receptacles or technology-ready for if and when DC gets “We are taking a step up to produce plugs, with gender choice. considered seriously.” the world’s highest rated subsea matable The longest modular confguration for Materials technology has already come connector,” says Mike Marklove, director a single phase 45kv connector will be a long way, but it has further to go, he of technology and innovation at Siemens about 1.5m, comprising a CMI, plug front says. “We use a wide variety of materials,
Subsea. “It means a step-change in mate- end, receptacle front end, CMI gland, thermoplastics for insulation, oils and rials, the connector has to become bigger, cable gland, and jumper. fuids, elastomers, exotic alloys. Over the “We are aiming to have the connector to be able to take the forces that comes years, every single material has improved available by 2015 and fnish long-term with those ratings. It also represents to increase performance.” qualifcation testing by 2017,” Ashley says.
challenges within sealing—we need new Giving an example, Marklove says inventions in sealing to overcome some The connector work is being done at 254 SMO stainless steel was quite com- of the issues we have in sealing this up.” Siemens’ Subsea Connector Excellence monly used. “We have now evolved
The 45Kv connector will be rated to Center at Ulverston. Testing, including to a much higher grade super duplex 3000m water depth, for use in the SPG materials and corrosion testing, high stainless steel. This has been by a need
September 2014 | OE oedigital.com 80 078_0914_subsea3_siemens.indd 80 8/21/14 6:46 PM