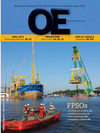
Page 82: of Offshore Engineer Magazine (Sep/Oct 2014)
Read this page in Pdf, Flash or Html5 edition of Sep/Oct 2014 Offshore Engineer Magazine
pro? le. Formulations showing a satisfac- tory cure pro? le and ? nal mechanical properties were then screened for prop- erty development using reactive rheom- etry and transient compression testing.
Pipelines
Innovating
The screening process narrowed our candidates down to ? ve formulations that showed the most promise. These formulations underwent further lab-scale ? eld joint insulation testing measure the rate of development possible, up from the standard ±1% by of rheological and mechanical proper- weight, to make the formulation more ties. The three most promising formula- forgiving than all previous ? eld joint tions were selected for evaluation at the coatings. pilot scale, where a plural component •
Faster build of compressive strength polyurethane machine was used to – all parties wanted a faster build of injection mold and bond X760E to a two mechanical properties contributing to inch thick coating of Dow HYPERLAST more ef? cient onsite pipeline assembly. DW512/300E GSPU on a two inch diam- •
Strong adhesion to various substrates – eter pipe. primarily the fusion-bonded epoxy (FBE)
Pilot-scale testing anti-corrosion coatings and the glass syntactic polyurethane (GSPU) “parent” Pilot-scale testing was carried out at coatings on the pipe sections. Dow’s application center in Birch Vale, • Mechanical and aging performance UK. Full-sized, industry standard equip- equivalent to legacy Hg-catalyzed systems ment was used to produce, mix and apply – subsea ? ow assurance coatings must the test materials, as would happen in withstand thousands of hours of service. the ? eld. These larger samples were then subjected to the same series of tests per-
Laboratory screening and testing formed in the laboratory, including adhe-
Dow’s research and development team sion, cure pro? le, compressive strength, Dow Chemical discusses the initiated an experimental program to assembling pipelines. hardness, and thermal conductivity. deliver against these customer require- When the use of mercury catalysts Based on this testing, XUR-07031977-760 development of non-mercury- was phased out several years ago, the ments. Starting in April of 2012, a series catalyzed ? eld joint insulation
Figure 2: Thermal property comparison industry responded with a variety of of different catalysts, chain extenders, ? eld joint formulations manufactured polyols, and isocyanates were screened
HYPERLAST™ material for subsea pipelines
Property MeasureXUR-07031977-760 FJ589 using non-Hg catalysts. While these ? rst- at laboratory scale in Freeport, Texas, generation, non-Hg ? eld joint formula- using a multi-variable design of experi-
Hardness Shore A 86 – 94 86 – 92
By Amber Stephenson, Dave Parker, tions worked well enough, none of them ments to ? nd formulations that matched
Tensile strength MPa =10 12 quite matched the performance of legacy or exceeded the cure pro? le, property
Mike Huspek, Kamesh Vyakaranam,
Elongation at break % =100 220
Hg products. The most elusive property build and ? nal performance characteris- and Mark Whelan.
Nicked crescent tear strengthN/mm =30 45 was rapid development of compressive tics of the legacy Hg-catalyzed ? eld joint
Density Kg/m31050 – 1165 1100 – 1150 or decades, offshore applicators strength and other mechanical properties coating. of ? eld joint insulation materials after application, [such as tensile and Formulations were ? rst screened to
Taber Abrasion mg loss =250 =250
F relied on the high performance tear strength]—which can potentially ensure that the cured elastomer provided
Thermal conductivity W/m·K =0.195 =0.195 characteristics of formulations contain- slow the onsite assembly of pipelines the requisite thermal and mechanical
Speci? c heat capacity J / g·K 1.4 – 1.7 ~1.5 – ~1.9 ing mercury (Hg) catalysts. Among the signi? cantly. properties. Cup calorimetry was then
NOTE: During customer Interviews, applicators requested minimal values on technical charts rather than more critical performance characteristics used to optimize catalyst type and load- typical values. Values shown for HYPERLAST FJ589 are typical or average values. Values shown for XUR-
Critical customer requirements of these Hg-catalyzed ? eld joint materials ing, to provide the desired cure time and 07031977-760 are minimum speci? cations.
were outstanding adhesion to different Dow Oil, Gas & Mining set out to develop substrates, outstanding hydrothermal a second-generation, non-mercury cata-
Figure 1: Compressive strength aging, robust processability, fast-build of lyzed ? eld joint coating, that matched build over time comparison 80 compressive strength, and other mechan- or exceeded the performance of our 70 ical properties. own legacy formulation—HYPERLAST
Pipe sections are connected by ? eld FJ589 Polyurethane. The ? rst step was to 60 joints in a multi-step process where the formally survey customers across the off- 50 slowest step determines productivity—so shore value chain, including applicators, 40 minimizing cycle time for application lay contractors, and offshore owners/ 30
Stress (psi) of the ? eld joint coatings is critical. operators. This gave us four primary per- 20
HYPERLAST FJ589
Legacy Hg-catalyzed ? eld joint coatings formance targets for a second generation, 10
XUR-07031977-760 typically exhibited rapid compressive non-mercury catalyzed ? eld joint coating: 0 05 10152025 • strength buildup, which optimized cycle Easy processing – applicators asked
Time (min) times to enable high productivity in us to widen the mixing tolerances if
September 2014 | OE oedigital.com 84 000_0914_Pipelines-1_DOW.indd 84 8/21/14 3:35 PM