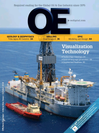
Page 44: of Offshore Engineer Magazine (Oct/Nov 2014)
Read this page in Pdf, Flash or Html5 edition of Oct/Nov 2014 Offshore Engineer Magazine
equipment manufacturers sign- ing off speci? c CAD designs that allow users to print to a speci? cation, which can then be
EPIC signed off or veri? ed to be meet- ing the speci? cation through a measurement and materials point of view.
Some of the issues could be resolved around using an enterprise resource planning (ERP) system, which contains information including when and how something was discov- ered to who the vender is, who the pattern makers are, suggests
Anderson. “When you are look- ing at adopting 3D printing as a signi? cant part of the procure- ment puzzle, you will have to think about treating the design as a piece of the inventory, look- ing at how they are stored, who the author is, what permissions there are, how to test it, how
Above left: A 3D-printed core sample. Right: A 2D core sample visualization.
Photos from Professor Franek Hasiuk.
to make sure they are aligned to original equipment manual
Samples for testing additive manufacturing in the oil and gas and warranties. Essentially, if you have
Hasiuk wants to take 3D core sample industry is printing onsite, which would people printing parts on site, it will printing a step further, by building vir- open up the potential to lower costs and either be done in an organized manner, or tual samples from the ground up, based increase staff safety.” as needed, which can lead down a route on CT scans, but modelled to create This could be bene? cial, as increasing to where no one has any idea about what homogenous samples and then printed numbers of ? elds are in more and more is operating on your asset.”
Another big piece of work will be and used to calibrate reservoir models remote, deep, and politically and geo- assessing what can and cannot be 3D through physical testing. You would be graphically hard to access places, with printed and when it might make eco- able to specify porosity, permeability storage and logistical hurdles. “There nomic sense to do so, something Wipro and surface area, then print it for test- would also be bene? ts in not having to is looking to help ? rms manage. The ing in a laboratory before calibrating a transport parts, and being able to tailor total cost of a part, including transpor- numeric method, Hasiuk says. It is work the parts on site to the particular applica- tation and storage costs, spillage rates, in progress. tion,” he says. down-time, and HSE risk, etc., now
A further development could see But, he adds: “Right now, there are need to be taken into account, Anderson purely computer-based models, or a lot of hurdles. Some of them are just says. “There are a lot of variables to “digital rocks,” which recreate and mechanical issues, around the print- look at – how much it costs to buy a model samples in order to better under- ing. There is a very limited capability part, get it on site, keep it on site, and stand ? elds. But Hasiuk says by printing to print with multiple materials in the deploy it. Understanding all that, as models you are better able to prove the same printing run. Most are able to print well as understanding where we are quality of the process. a single material and print different parts technologically with 3D printing, allows
As patents on 3D printing lapse, and then assemble them later. Also, the us to see what is possible in terms of particularly Selective Laser Sintering time and expense printing a single object what is proven (in terms of printing, and methods which enable the use of can take hours or days. There is also a lot
IP, and warranties) and from that we minerals in 3D printing, further doors more ? nishing and post-printing work can create a list of what is possible and will open, he says, both enabling print- that needs to be done.
where 3D printing could be more cost ing with different materials, but also “There are also legal issues, some effective than purchasing and transport- enabling control of surface texture. This to do with IP, some with warranty. As ing a part on site.” could allow much more accurate surface far as I know, people are still trying to physics. address how you might keep a warranty “I think that as the technology valid if you use 3D printed parts printed improves, it is possibly going to make
Printing on site yourself. Even a simple part swap might more and more sense to print things
Chris Anderson, director, innova- negate a warranty. I think all these things locally, especially when you look at costs tion and applied technology at Wipro will be resolved, but I don’t think they and risks associated with transportation
Technologies, based in California, says: this will happen until they are tried.” to some of the sites where our industry is “The obvious potential for 3D printing or A potential scenario could be original working. But it will take a while.”
October 2014 | OE oedigital.com 46 044_OE1014_EPIC1_3D.indd 46 9/23/14 1:46 PM