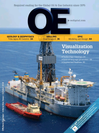
Page 60: of Offshore Engineer Magazine (Oct/Nov 2014)
Read this page in Pdf, Flash or Html5 edition of Oct/Nov 2014 Offshore Engineer Magazine
to perform buried pipeline detection, and free span detection and measure- ment, using laser scanners or multibeam echosounder. It would also need to detect
Subsea global and local buckling, and pipeline movement, using post processing of imagery, AUV navigation and laser/mul- tibeam cross sectional pro? les, Nasr said.
Cathodic protection surveys would be a requirement, to assess coating damage and anode condition, including anode current output. The AUV would need to perform seabed conditions using post processed laser or multibeam cross sectional pro? les.
Finally, Total has an outline speci? ca- tion for mission reporting. It says the
AUV’s system would need to include
Screenshot composite photo taken during the AIV trials, showing the AIV docking into providing a comprehensive inspec- its basket autonomously, sonar imagery and a still from the monitoring work class ROV.its basket autonomously, sonar imagery and a still from the monitoring work class ROV.
tion report, standard ROC and sonar to use HD stills cameras and strobe light- inspection type deliverables, as well as
Scan this page!Scan this page!
ing synchronized to each photograph. mosaicked, geo-referenced HD pho-
Scan this page with your smart phone
The images would then be mosaicked tographic data, geo-referenced sonar or tablet and the Actable app to ? nd to create a continuous, geo-referenced mosaic, 3D rendering of laser or multi- out more about Subsea 7’s new AIV image of the pipeline. beam echosounder cross sectional data, technology.
For free span detection, mechani- and GIS format delivery. have never been done by AUV before.” Nasr says such a system should be cal pro? lers (or dual beam multibeam
Sensor power and payload require- echosounders) are used, and sonar able to travel a minimum 100km in one ments, control, maneuverability, and processing. But there is a need for faster mission. “The sensors and technology are complexity of operating fully autono- surveys, Nasr said. He suggests using available, but the challenges are to accom- mously, are also challenges, he said. laser scanners, creating a 3D rendering of modate them to meet AUV pipeline inspec-
Navigation has traditionally been the pipeline and seabed relationship, or tion needs,” he said. He hopes the outline vessel-based acoustic positioning, with high frequency sonar (multibeam) offset speci? cation will provide guidance on a pre-determined route and ROV visual from the pipeline, with bathymetry and operator requirements to the AUV industry, piloting. The challenge with this approach sonar backscatter processing. The bene? t but that it could need to be modi? ed to is ability to perform real-time feature- of a laser scanner would be not having meet improvements in sensor capabil- based navigation to pipeline features and problem with frequency management. ity, and changing integrity management not being able to operate without a surface The challenge is understanding laser requirements from operators or regulators.
vessel, Nasr said. An alternative, AUV- scanners underwater, Nasr said.
Future systems based approach, is to use pipeline recog- For corrosion surveys, a direct stab of nition and subsea features positioning, the cathodic protection anode is currently “For future systems, we could have a using an onboard-stored map on the AUV. used, which has autonomous identi? ca- docking station for communication and
SeeByte in Edinburgh has already been tion, stab accuracy and reference cell loca- power, linked to a host platform (a ? eld working on such a system, which is used tion challenges, Nasr said. An AUV-based resident system). The AUV will send its in commercially available ROVs, includ- option would be contactless cathodic data for evaluation and collect new mis- ing SMD’s MKII Quasar. FMC Schilling protection using data harvesting—with sion details,” Nasr said.
Optic transceivers could also be incorpo-
Robotics uses its own Station Keep visual a sensor transmitting data which can be rated into subsea processing systems and recognition technology. harvested by the passing AUV. downloaded at short range at 10-50mb/s
Challenges with such a system include
An outline speci? cation data rates. This would also allow the AUV “blind spots,” where there are a lack of
Total’s outline speci? cation incorpo- to be controlled real time, wirelessly. seabed features, which would make the rates using HD stills cameras to visually auto tracking dif? cult. A solution could A key function will be hydrocarbon inspect the full length of the pipeline, in be tridents installed on the seabed to leak detection, he says. If it detects a leak conjunction with a strobe light, with high aid navigation and this is seen as being it will abort its mission and either return frequency multibeam sonar, taken at a future standard practice, Nasr said. to look at it again to better characterize the ? xed offset and consistent aspect angle
Another challenge is visual inspection. leak, or resurface or go to a docking sta- reference from the seabed. These would
This is usually carried out using a video tion to report the incident. Riser inspec- be used to identify damage or anomalies, streams, using three video cameras, two tion could also be a future addition. debris, and pipeline features, through located on booms, to show the pipeline The next step would be simple tooling, post-processing of laser or multibeam data. to seabed interface. This uses a lot of data he said. “If we are able to control it, you and power for continuous footage, as Pipeline tracking would be via visual could have assembly tooling to do assem- well as lighting and the need to be close recognition and or laser/multibeam bly tasks. The ultimate goal is to reduce to the pipeline. Nasr said an alternative is data in real-time. The AUV would need the work of the support vessel.”
October 2014 | OE oedigital.com 62 000_OE1014_Subsea3_AIV_v3.indd 62 9/23/14 4:51 PM