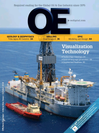
Page 65: of Offshore Engineer Magazine (Oct/Nov 2014)
Read this page in Pdf, Flash or Html5 edition of Oct/Nov 2014 Offshore Engineer Magazine
SubseaEyebrow
Work? ow of the Backup Bearing function design using Multiphysics/Multiscale Simulation.
on local contact problems and allows for
Subsea Compressor Module Architecture - AMBs/ studies of dynamic behavior of all bear-
Controller. Image courtesy of Aker Solutions and GE Oil & Gas.
ing components to be carried out under general loading conditions. Principal out- put data from BEAST relates to the move- ments of all bearing components, the contact forces between the components, and the forces with the environment.
BEAST also provides detailed data from the contacts regarding smearing power, lubricant ? lm thickness (of any type), pressure distribution, slip-speed distribu- tion, transient temperature distribution, wear and many other factors.
Tools validation
Simulation results and drop test data comparison (position signal K1 bearing).
Tools validation was achieved by build- ing a reduced scale compressor test-
Ormen Lange land facility seen from the (cartridges) where one of the challenges prohibitive in terms of both cost and cal- bench, carrying out a landing test cam- air. Photo: Svein Roger Ivarsen/Shell.
was to use canned bearings for protect- culation time. M2S2 provides an answer paign, and ? nally comparing the data especially by means of appropriate mod- ing the stator coils (bearings and sen- to this problem. It allows the superposi- collected with the simulation results. eling/simulation tools that are able to sors) from any contaminant present in tion of the different physical and scale
The shaft of this test-bench (200kg) was loop on the requirements issued by the the cooling gas. One of the issues to be domains, providing both an overview of designed for supercritical operation stakeholders. addressed was the validation of predic- the system and the ability to zoom in on and therefore needed to be ? exible. In
The project development phase was tive behavior of the thrust bearing and speci? c areas to predict system behavior. contrast to the full scale compressor, deployed using M2S2 (Multiphysics/ auxiliary bearing during the production Backup bearings can be considered the test-bench rotor was con? gured
Multiscale System Simulation). This life cycle of the machine; constraints as an “airbag” for machine integrity. horizontally, driven by a motor on the methodology provided all project stake- and speci? cation of axial load during During rotor drop, part of the “mechani- shaft end bearing. Bearings 1 and 2 holders with behavioral models, each a rotor drop and external force pertur- cal phenomena” that occurs is measured were ? exible mounted angular contact compromise between the details of physi- bation were given by the compressor in the range of the system’s spatial bearings that act in radial direction cal behavior and complexity. maker as well as the axial bearing load scale, particularly in terms of rotor/sta- only, while bearing 3 was an angular capacity of 45kN, whereas the radial tor interaction. Process and rotor/stator contact bearing supporting radial and
The Ormen Lange pilot project bearings 1 and 2 had a 16kN load capac- perturbations are applied in real-time to axial loads.
During the landing test campaign, the
The subsea compression station at ity and the radial bearing 3 had a 7kN backup bearings, generating extremely
Ormen Lange comprises a “main load capacity. complex phenomena (friction, deforma- axial loads were generated by the magnetic module” equipped with two or The designers faced a wide range of tion, heating) inside the bearing itself, thrust bearing, situated between bearings four 12.5MW subsea compres- challenging physic ? elds, including all occurring within very different spa- 1 and 2. This axial load was applied in direction of bearing 3 and immediately direction of bearing 3 and immediately sion units. The integrated vertical mechanical, electrical, magnetic, ther- tial scales that range from micrometers generated a forward whirl.
motor-compressor (max speed mal and many others where the electri- to centimeters. 11000 RPM) is equipped with cal time constants (< microseconds to An SKF in-house tool called BEAST
Scan this page!
AMBs (three radial bearings and a milliseconds) are usually much smaller (BEAring Simulation Tool) provides a
What new subsea technology has thrust bearing) linked to a variable than mechanical ones (several millisec- fully geometrical 3D model incorporating potential to make the most impact? speed drive, a separator module, a onds to seconds). Taking into account tribology and contact mechanics (which
Tell us what you think. Scan this page with cooler, and a liquid pump. all these phenomena in numerical simu- also takes into account the effects of your smartphone or tablet and the Actable
The motor compressor is lations requires using extremely detailed small-scale geometric variations, such as app or visit svy.mk/1p4uMBK. Find the equipped with three main active models, and different types of solutions surface roughness). BEAST is based on results in our December 2014 issue.
magnetic bearing modules resulting in a calculation process that is multi-body techniques with special focus oedigital.com October 2014 | OE 67 066_OE1014_Subsea7.indd 67 9/24/14 1:14 AM