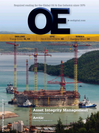
Page 30: of Offshore Engineer Magazine (Nov/Dec 2014)
Read this page in Pdf, Flash or Html5 edition of Nov/Dec 2014 Offshore Engineer Magazine
ASSET INTEGRITY MANAGEMENT
Aging infrastructure
Simon Frost explains the role of engineered composite repairs in late life asset management. under wraps costly and might not be deemed good value for a platform near- ing decommissioning or where bed space offshore is limited, as replacement can require additional manpower over relatively long periods.
Engineered composite repair solutions
Engineered composite repairs offer an alternative solution and can be completed in shorter timeframes. Composite repairs have been used offshore for a number of years, primarily on pipework with localized corrosion defects, but also in tanks and vessels. However, the engineering principles are also valid for the repair of structural components.
Composite repairs are governed by ISO/TS 24817 or ASME
PCC-2 Article 4.1 standards, which defne the qualifcation requirements, design rules, installer training requirements and installation guidance.
Composite repairs are used for a number of reasons. First, no hot work is required – an important beneft when offshore safety requirements render hot repair solutions impractical.
Second, once applied, composite repair systems are corrosion resistant and can be guaranteed for up to 20 years – poten- tially the life of the feld. Furthermore, if the corrosion on the structure is external, applying the repair will prevent further material loss. Third, in some instances it is possible to apply a repair while the pipework is in service, allowing production
A tubular brace, having sufered wall to continue. Finally, composite solutions can be used to repair loss through external corrosion, was most defect types in the offshore oil and gas environment. The reinstated to its original fexural strength with an engineered structural only defect type where careful consideration is required is composite repair. Photos from Walker Technical. crack-like defects.
The technology he North Sea’s aging assets pose a number of challenges A composite repair consists of two main components: a com- for the industry in the UK. Several assets on the UK posite laminate (either an impregnated carbon or glass cloth
T
Continental Shelf have been in operation for 30 years with a thermosetting resin, e.g. epoxy or polyurethane) and an and are expected in some instances to remain in service for a adhesive (either an epoxy or polyurethane resin). further 20 years. Recent fscal changes, including a brown feld A critical aspect of the installation process is adhesion, tax allowance and greater certainty on decommissioning costs irrespective of the specifc application. In most cases, the per- through the decommissioning relief deed, will likely lead to an formance of the composite repair is not limited by whether the increasing number of asset life extension projects. repair can withstand the applied loads, but whether the loads
Operators should recognize that the structural integrity of can be transferred from the underlying pipework or structural an asset needs to be maintained during its operational life and component into the composite laminate. To transfer the loads, even after cessation of production, through any unmanned the adhesive layer between the component and composite phase and preparations for removal, until the asset is fnally repair must withstand and carry out this transfer. Therefore, it removed. This means structural integrity, subsea, in the splash is crucial to understand the parameters that infuence adhesion. zone and on topside structures, including components such as There are fve main factors for consideration. These are: • pipes and pipework, beams, decks, struts, stairways and towers, Surface preparation • must be closely monitored, maintained, and plans made for Component material • their continued safe operation. Surface cleanliness •
While operators have the option to replace components, the Repair material – primarily the resin • evolution of many assets has rendered some components inac- Environment – humidity, dew point temperature cessible, making replacement diffcult. Replacement can also be The most important parameter is surface preparation. To
November 2014 | OE oedigital.com 32 032_OE1114_Asset3.indd 32 10/20/14 10:23 PM