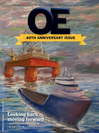
Page 45: of Offshore Engineer Magazine (Jan/Feb 2015)
Read this page in Pdf, Flash or Html5 edition of Jan/Feb 2015 Offshore Engineer Magazine
EPIC
The Rhum field layout senior well integrity engineer at BP. A third Rhum production well, which had failed before starting production, had a downhole pressure gauge. “Throughout the four years we knew what the pres- sures were down there, so we always had eyes on it,” Labroo says.
In some shut-in ? elds, pressure build up can be expected, if there is pressure
The Rhum ? eld location support from water, for example. Rhum, in the UK North Sea however, stayed relatively stable, at just under 8000 psi, close to the level it had been when it was shut-in, Labroo says. “The fascinating thing was challenges around the hardware, proving it all worked,” says Scott Forrester, project manager, Rhum restart, BP. “Up until that point, we had been restricted on what level of maintenance we could do on the system, meaning that no preservation on the equipment could be carried out. Safety and Operational Risk (S&OR) export speci? cations, Rhum had to
We used our maintenance management team, and a number of engineers who ? ow more slowly, because Bruce rates system and took time to understand all had previously worked on the ? eld to had declined since Rhum ? rst started- of the work we should have been doing provide a peer review of the activities the up. Reduced ? ow rates meant cooler (but couldn’t) over the past four years. existed prior to shut in, but where, for team were undertaking. “Because it had operating conditions in the pipeline,
We also took time to understand where the same reasons, we had been unable been shut in for four years, and things which meant assumptions in the original equipment reliability challenges had to take advantage of the four-year shut- would have understandably changed in Rhum HAZOP and LOPA also had to in period to work on removing these that time, I made sure we had a lot of be checked, and updated, to re? ect the issues.” people looking at this,” Forrester says. changed regime.
Safety critical, environmental criti- The Department of Energy and Climate One of the key considerations was cal and production critical work scopes Change, acting as the manager of IOC’s hydrate formation, says Stephen Blaney, were prioritized with the aim to bring share of the ? eld, were also involved. ? ow assurance engineer, BP. “Rhum is back the facilities to the “status quo.” In Because Rhum’s topsides facilities are predominantly gas, with a bit of water. addition, the entire system topsides and on Bruce, function testing and proving Together with the length of the tie-back, subsea system was assessed by a multi- all the equipment had to take place at this makes hydrate formation a risk,” discipline team of engineers, including the same time as having to accommodate he says. “To manage it, a mix of design the manifold and high-integrity pressure for the fact that there were other priority features were agreed for the [original] protection systems, to return the whole operational activities on the Bruce plat- facilities.” system from its unpreserved state, in form, not necessarily aligned to Rhum’s To mitigate hydrate formation during a manner that was safe and compliant restart. “It was a careful balance, as the normal operation, the pipelines from the with BP engineering standards, involving Bruce platform, as host to Rhum facili- controls to the manifold and the 44km the function testing and proving of all ties, had to be reliable so that we could pipeline from the Rhum manifold to equipment. be con? dent to ? ow Rhum ? uids during Bruce, which is also buried, is an insu- “We took a view that we had just the critical cold start period. Any upset lated pipe-in-pipe system. On a normal installed it and we needed to prove all on the Bruce facilities would have been a shut down, any water that drops out is the equipment was ? t for purpose again,” problem,” Forrester added. gravity-drained into even more highly
Forrester says. Functional experts from There was another consideration for insulated sections of the pipe, to slow across the business supported the restart the restart. Because of the need to blend down any cooling, so start-up can resume with assurance measures, as well as BP’s Rhum gas with Bruce gas, to meet CO while the liquids are still relatively 2 oedigital.com January 2015 | OE 47 046_OE0115_EPIC1_Rhum.indd 47 12/22/14 6:54 PM