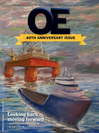
Page 54: of Offshore Engineer Magazine (Jan/Feb 2015)
Read this page in Pdf, Flash or Html5 edition of Jan/Feb 2015 Offshore Engineer Magazine
by managing fles in ProjectWise. the UK North Sea. With an 88m X 62m and 10 pipe racks within 10 months.
Effciencies achieved during detail footprint on the seabed, the 120m-high
The company used SACS for modeling, design saved 5000 man-hours of the jacket supports a topside facility analysis, and optimization of the FPSO 30,000 engineering hours. weighing around 54,000t. The jacket’s topside structure and STAAD.Pro to
EPIC
Simulations conducted using MOSES weight and subsequent installation design its tertiary steel. SACS achieved and SACS cut the estimated topsides by barge were signifcant challenges. a 10% overall reduction in steel weight ?oatover time from four days to two days. Using SACS and STAAD.Pro, SNC- per module/pipe rack compared with
Safety considerations during simulations conventional design. SACS provided allowed the installation to be performed clear visualization of lifting arrange- ments and detected structural clashes. without incident. Being able to trans-
STAAD.Pro’s helped the team complete fer data between SACS and MOSES the project on time.
increased project effciency.
With a vertical center of gravity 48.3m
Vessel design above the keel, the topsides’ stabil-
In addition to MOSES and SACS, Bentley ity requirements pushed the limits of also has a vessel design system called the installation barge, HYSY 229. The
MAXSURF for the initial hull design of bottle-shaped barge made the ?oatover new vessels and review of stability for operation feasible because it satisfed modifcations to existing vessels.
both the stability and jacket footprint
Having SACS and MOSES in the same requirements. However, it created chal-
Statoil’s Mariner jacket. company has lead to enhanced interop- lenges for the mooring arrangement and
Image from SNC-Lavalin. erability, says Bentley. There is also transportation global strength needs.
The short, fat, and heavy jacket full integration between SACS and also brought challenges to the
ProjectWise, and mechanical/struc- launch operation.
tural integration between AutoPipe
The runners up for the award and SACS. There are plans for the were Orca Offshore’s transporta- future to create i-models automati- tion and installation analysis of the cally, and for increasing use of cloud
F3-FA self-installing platform and computing. I-models are a medium
SNC-Lavalin’s Mariner feld devel- for information exchange within opment detailed design project. projects associated with the lifecycle of infrastructure assets. They facili-
A Dutch Orca tate the sharing and distribution of
Orca Offshore performed trans- information regardless of the source port and installation analyses for and format of the information.
MOSES semi-submersible mooring
Bentley says it continues to invest
Centrica’s £200 million self-installing gas analysis. Image from Bentley Systems.
in product development, with major platform in the Dutch sector of the North releases every nine months or so.
Sea. The F3-FA platform has a suction
MOSES V7.1 was released in September pile foundation resting on a temporary Lavalin completed the jacket design in 2014. Christensen says: “This frst barge for transportation. It can be relo- a tight timeframe. Nineteen interrelated major release of MOSES since Bentley cated, providing signifcant cost savings analyses were performed effectively acquired it in October 2013 increases across three to four felds. using SACS’ various modules, including the software’s interoperability and
Orca’s scope of work included motion wave-loading under storm conditions, extends the resulting information mobil- and stability analysis, multi-body seismic response, fatigue, sea-transpor- ity. For starters, it offers an enhanced dynamic analysis, structural spectral tation, and accidental impact. STAAD.
ability to import SACS structural analysis, and scale model tests. It was Pro was used for the detailed design models into MOSES, along with the crucial to know hydrodynamic loads of secondary steel. Working with the automated generation of SACS loading early in the project due to the pile size same software as the topsides designer fles from MOSES – enabling collabora- – 15m-high and 15m-diameter – and enabled effcient information sharing tive work?ows among offshore struc- proximity to the wave zone. The loads and modeling of the interfaces between tural engineering and naval architecture determined how to size the steel work. jacket and topsides.
Bentley also highlighted the OSX-3 teams.
MOSES determined those loads and topside design, which was a fnal- confrmed the structural strength of the “In addition, through MOSES V7.1’s ist for the Be Inspired award in 2013, platform. The use of MOSES reduced the support of integrated structural model-
Bentley software helped reduce the amount of steel required in the platform ing, users are able to work within inte-
OSX-3 FPSO topside steel weight by and for sea fastening and proved grated and ?exible structural modeling, 10%. L&T-Valdel Engineering, head- analysis, design, documentation, and
Engineering Mariner quartered in Bangalore, was commis- detailing work?ows. This gives them
Statoil awarded SNC-Lavalin the front- the advantages of intelligent structural sioned by MODEC International to end engineering design contract for design practices, which can help them provide modularization design for the
FPSO topside. The challenge was to its massive 22,000t jacket at the US$7 deliver offshore platforms faster while complete the design of 15 modules billion Mariner oil feld development in reducing project risks.
January 2015 | OE oedigital.com 56 054_OE0115_EPIC3_Bentley3.indd 56 12/22/14 7:00 PM