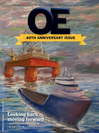
Page 64: of Offshore Engineer Magazine (Jan/Feb 2015)
Read this page in Pdf, Flash or Html5 edition of Jan/Feb 2015 Offshore Engineer Magazine
optimum potential. That is where Shell’s
Bridge team comes into play, so they can use automation technology to ? x the small problems.
The use of the reliability technology helps alleviate the problems that opera-
Automation tors have learned the hard way.
The new technology allows them to con? gure their systems to understand where past problems cropped up. “They are continually adding additional rules and algorithms to monitor and look for different kinds of or new conditions,”
Winters said.
0 1 0 1 1 1 0 0 1 0
Remote reliability 0 1111111111 1 00000000000000000000000000
Monitoring systems is not just a one per- 0000000000 son proposition, and as Shell determined, it takes a large cast. That is why remote monitoring is playing a bigger part in the reliability picture moving forward. “We are doing two deployments in the
North Sea and both of those are mov- ing to a remote operations scenario,”
Winters said. “Their goal is to reduce the amount of bodies on the platform, one of the implications is they will have fewer maintenance people on the platform.
When they are sending someone to the platform they can know which poten- tial instruments are having problems,
Bridge and what pumps are having problems, they can be more proactive around that and do better maintenance scheduling.
Technology is bringing in health informa- to tion from the smart instruments, electri- cal systems, rotating equipment, and choke valves. That is one way to be more proactive around optimizing the wrench time when going out to the platform.”
Reliability
The whole idea behind remote moni- toring of equipment on the platform is to
New age technologies head off any issues for the critical assets. and compare that to the last 15min aver- problem-solving engineers working on “What you are able to see is a rate of block failures, and age and if they see a spike or a sudden speci? c ? xes and projects. The goal is to degradation on any of the equipment boost bottom line. change, that will trigger a surveillance catch and ? x small issues and alert those on what you characterized as the failure task and a group of engineers comes in on the platform when they ? rst crop up modes and how you have characterized
Gregory Hale reports.
and investigates what might be caus- as a seemingly innocent bit of data before the degradation mechanisms,” said Stan ing that sudden change. Preventing a they become an issue. Grabill, principal reliability consultant catastrophic compressor failure is worth “They are monitoring the rotating very minute counts these days. at HPS. “So, it is not just seeing it hours about $4 million to them. In another equipment and also some of their process The right decisions hinge on before it fails, but rather getting early
E case if they trip a compressor and have equipment and looking for various lead- responding to issues before they indications or early event detection. In an event ? aring for a four-hour period in ing indicators of degradation of equip- become big, costly problems. The idea some cases we can have an interven- downtime, it can save them multiple mil- ment health,” said Bart Winters, product of equipment reliability is becoming an tion without severe degradation or can lions of dollars.” director for asset management solutions even more vital factor offshore. recover the degradation with some
Tom Moroney, manager of deepwater at Honeywell Process Solutions (HPS). This is why Shell created a team of proactive maintenance. You can accumu- technology and geosciences at Shell “They are seeing signi? cant savings by engineers at its Upstream Americas late this information across an array of spoke at the Honeywell User Group in being able to set up monitoring systems, deepwater headquarters in New Orleans assets whether they are electrical rotating
June 2013 about the hike in technical like in the case of turbine exhaust gas overseeing 300 wells and about 12-13 machinery, heat exchanger performance, and business complexity along with the temperature, that look for a sudden rate main platforms in the Gulf of Mexico. where you get input on performance workforce demographics and techniques of change in the exhaust gas temperature. They act as a bridge between platform you can see anything that is starting to on utilizing the resources they had to the They will look at the last month average operators running equipment and go south on you. The software is set up
January 2015 | OE oedigital.com 66 066_OE0115_automation.indd 66 12/22/14 11:12 AM