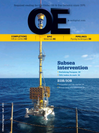
Page 46: of Offshore Engineer Magazine (Apr/May 2015)
Read this page in Pdf, Flash or Html5 edition of Apr/May 2015 Offshore Engineer Magazine
chemicals. The combination of these conditions, generally those stated in the involving several samples that will be variables with crude or gas typically international standards. Few qualifca- immersed in the liquid/gas mixture results in a harsh environment where tion programs take into consideration the under HPHT. The tests can last from days materials selection is critical and where real environment in which the materials to months and in some cases the samples
EPIC corrosion monitoring, from wells to will be operating and typically have a are totally disintegrated at the end of the production and processing facilities, may poor understanding of the acceleration tests. Therefore, no assessment of the also be required. factors for their basis of qualifcation. expected lifetime of the metal can be
Top of the line corrosion (TOLC) is an
For example, using constant load done using weight loss and no assess- example of a harsh environment ment of the type of corrosion that arises with the transport of mechanism can be done on the hydrocarbons with water (and coupons.
gas) resulting in water conden-
Ideally, the metals should sation in the upper part of the be observed during the test to pipeline, where the corrosion identify the onset of corrosion inhibitors contained in the fuid (for example general corrosion cannot inhibit corrosion in the or localized corrosion) while gas phase. Corrosion modeling the sample is immersed in the can assess the most susceptible
HPHT harsh environment. areas along the pipeline and
This can be done through a assist to select the use of corro- new methodology using a sion resistant alloys (CRAs) or mini-autoclave that allows other engineering strategies to concurrent and in-situ micros- mitigate TOLC.
copy and electrochemical tests
Fig. 2. In-situ microscopy and electrochemical testing at HPHT
Another prevention method in real time.
in sour environments. Image from NACE Paper C2012-0001514.
used during operation is cor- In Figure 3, the sample was rosion monitoring. Typically, heated to 180°C (356°F) in this would involve coupons 20,000 ppm chloride (40 bar or online monitoring systems, CO , 0.025 bar H S and 0.02 M 2 2 although more innovative meth- CH COOH). Pitting corrosion 3 ods are currently being devel- was confrmed both visually oped as alternative monitor- and in the electrochemical ing. For example, a good fow signature.
assurance program can predict The advantage of using this extreme environmental condi- technique is that it provides
Fig. 3. Microscopy and electrochemistry at 180 C (356 F) in 20,000 ° ° tions that can impact the cor- real-time visual confrma- ppm chloride (40 bar CO , 0.025 bar H S and 0.02 M CH COOH) of 2 2 3 rosion processes taking place tion of the processes (corro- a duplex stainless steel. Image from NACE Paper C2012-0001526.
while the hydrocarbon is being sion, degradation, microbial transported. There is a strong incentive to testing (which is simple and widely attack, etc.) that happens in the material use more than one methodology for corro- understood) generally oversimplifes the inside the autoclave while the sample sion monitoring. problem and cannot address corrosion is immersed in the HPHT harsh envi-
Typically, corrosion monitoring fatigue under the real cycling conditions. ronment. Another advantage is that the doesn’t shed light on the corrosion
Similarly, other tests such as slow strain material can be monitored over time and mechanisms taking place within the rate testing (SSRT), which is aggressive video recording can be used to compare harsh environment; that is where corro- and rapid, can be too aggressive and it their interaction with the environment.
Marin provides comprehensive specialist services in the areas sion coupons, modeling and fow studies can be diffcult to determine if cracking However, this technique can only be
Nobody of full ocean depth excavation, can be an ally and complement one occurred inside service conditions. On used below 4000psi and 400°C (which recovery, decommissioning, another to provide meaningful corrosion the other hand, ripple strain rate testing is a limitation given by the materials of drilling and offshore support.
does it information. A good integrity manage- (RSRT) includes corrosion fatigue and construction of the window).
With a strong bias towards oil and gas frontiers, delivering complete ment plan can lead to cost savings by is adaptable, but with the drawback of solutions on complex projects
Challenges ensuring the selection of the right materi- being more complex and costly than deeper in the toughest and harshest of locations globally, Marin’s technology als and technology, and use of the correct constant load testing and SSRT. Still, all Many testing programs exceed 150°C is cutting edge with specialists that tools for corrosion monitoring during the of those methodologies need to take into (302°F), but range from 3000psi (206.8 thrive on solving deepwater lifetime of the asset. consideration the real environment and bar) to 15,000psi (1034 bar). New challenges.
should mimic actual conditions in order industry standards for HPHT are being
Testing and qualifcation to be acceptable as qualifcation methods. developed. For example, the current API
Downhole Subsea Offshore
Solutions Intervention Support for harsh environments 14A, Edition 11 standard for surface-
Mechanical and corrosion testing can controlled subsurface safety valves
In-situ testing to simulate internal corrosion in harsh environments be done using conventional techniques (SCSSVs) requires that SCSSVs with a
Subsea without limits.
and international standards. However, Corrosion testing in harsh environments, working pressure >10,000psi (689.5 bar) marinsubsea.com the typical qualifcation of materials which typically contain H S, CO and be tested to 5000psi (344.7 bar) above 2 2 for their use in extreme and/or harsh NaCI in a liquid/gas mixture, is typi- working pressure, rather than the 1.5 environments is usually done under ideal cally conducted in autoclaves at HPHT, times working pressure requirement of
April 2015 | OE oedigital.com 48
Marin_85x123_advert_Final.indd 1 20/01/2015 11:58 046_0415OE_EPIC1_Woodgroup.indd 48 3/23/15 4:22 PM